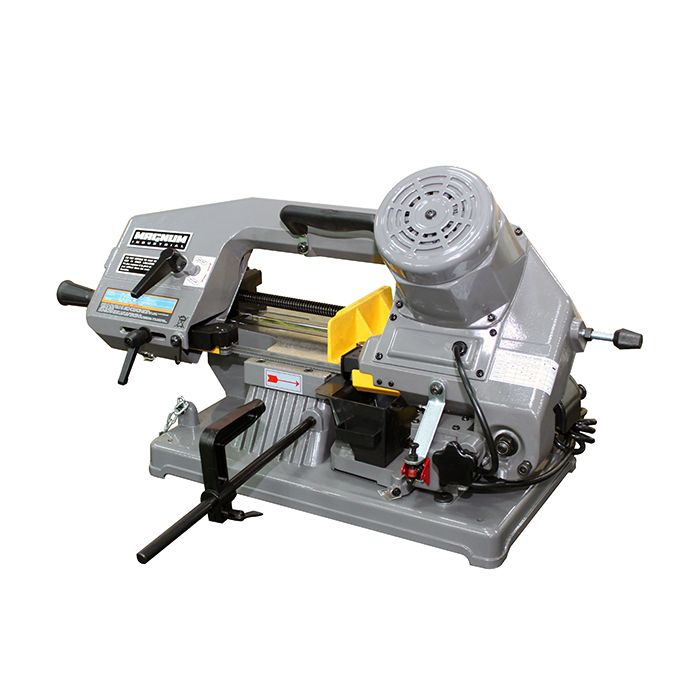
Metal Band Saws: The Cutting Edge of Precision Metalworking
Introduction: Unveiling the Power of Metal Band Saws
Metal band saws stand as indispensable tools in the world of metalworking and fabrication. These versatile machines cut through various metals with precision and efficiency, making them essential in industries ranging from construction to manufacturing. The core of a metal band saw consists of a continuous loop of toothed metal blade that rotates around two or more wheels, creating a powerful cutting action. This design allows for smooth, accurate cuts on a wide range of materials, including steel, aluminum, and copper. Metal band saws come in various sizes and configurations, from portable handheld units to large industrial models capable of cutting through thick metal stock.
Their ability to make straight cuts, curved cuts, and even intricate shapes sets them apart from other cutting tools. Additionally, metal band saws produce less waste and generate a smoother finish compared to many alternative cutting methods. As technology advances, modern metal band saws incorporate features like variable speed controls, automatic feed systems, and computer numerical control (CNC) capabilities, further enhancing their versatility and precision. Whether in a small workshop or a large manufacturing facility, metal band saws play a crucial role in shaping the metal components that form the backbone of countless products and structures. This blog post will delve into the world of metal band saws, exploring their types, applications, benefits, and the factors to consider when choosing the right saw for specific metalworking needs.
Types of Metal Band Saws: Choosing the Right Tool for the Job
Metal band saws come in several types, each designed to meet specific cutting needs. Vertical band saws stand as popular choices for general-purpose cutting tasks. These machines feature a stationary blade assembly, with the operator manually feeding the workpiece into the blade. Vertical band saws excel at making curved cuts and intricate shapes, making them ideal for custom fabrication work. On the other hand, horizontal band saws cater to cutting larger stock and performing repetitive cuts. In these machines, the blade assembly lowers onto the stationary workpiece, allowing for efficient straight cuts through thick materials. Many horizontal band saws include automatic feed systems, enhancing productivity for high-volume cutting operations.
Portable band saws offer flexibility for on-site cutting tasks. These handheld tools prove invaluable for construction and maintenance work where mobility is essential. Contour band saws specialize in cutting complex shapes and curves in sheet metal, often used in aerospace and automotive industries. For heavy-duty industrial applications, production band saws handle large-scale cutting operations with features like automatic material handling and computer-controlled cutting sequences. Bi-metal band saws utilize blades with high-speed steel teeth welded to a flexible steel backing, providing durability and versatility for cutting various metals. Carbide-tipped band saws offer superior cutting performance and longevity when working with hard or abrasive materials. Understanding the strengths of each type helps in selecting the most suitable metal band saw for specific cutting requirements.
Key Components: The Anatomy of a Metal Band Saw
Understanding the key components of a metal band saw helps operators maximize its performance and maintain the machine effectively. The blade serves as the heart of the band saw, with its design tailored to the specific cutting task. Blade teeth come in various configurations, including variable pitch for reduced noise and improved cutting efficiency. The drive wheel and idler wheel work together to keep the blade in motion and maintain proper tension. A robust motor powers the drive wheel, with more powerful motors enabling faster cutting speeds and the ability to handle thicker materials. The blade guides play a crucial role in maintaining blade stability and accuracy during cuts. These guides often incorporate bearings or ceramic inserts to reduce friction and extend blade life.
The machine’s frame provides structural support and determines the maximum cutting capacity. Many metal band saws feature coolant systems that flood the cutting area with lubricant, reducing heat buildup and extending blade life. The vise or workholding system secures the material firmly in place during cutting operations. Control panels on modern band saws offer features like variable speed settings, automatic shut-off, and digital readouts for precise control over cutting parameters. Some advanced models incorporate hydraulic or pneumatic systems for blade tensioning and workpiece clamping. Safety features such as blade guards and emergency stop buttons ensure operator protection. Understanding these components allows users to optimize their metal band saw’s performance and troubleshoot issues effectively.
Precision Cutting: Techniques for Optimal Results
Achieving precise cuts with a metal band saw requires proper technique and attention to detail. Selecting the appropriate blade for the material and thickness being cut stands as a crucial first step. Blade selection involves considering factors such as tooth pitch, set, and material. For most metals, a bi-metal blade offers a good balance of performance and durability. Proper blade tension plays a vital role in achieving straight, accurate cuts. Insufficient tension can cause the blade to wander, while excessive tension may lead to premature blade failure. Many modern band saws feature automatic tensioning systems to maintain optimal blade tension. Setting the correct cutting speed helps maximize cutting efficiency and blade life.
Softer metals generally require higher speeds, while harder materials benefit from slower speeds. Variable speed band saws allow for fine-tuning the cutting speed to match the specific material properties. Proper workpiece support ensures stability during the cut, preventing binding and potential blade breakage. For long or irregularly shaped workpieces, roller supports or outfeed tables provide essential stability. Using cutting fluid or coolant during the cutting process reduces friction and heat buildup, resulting in smoother cuts and extended blade life. When making curved cuts, it’s important to use relief cuts to prevent blade binding. These techniques, combined with proper machine maintenance, enable operators to achieve consistently precise cuts across a wide range of metalworking applications.
Applications Across Industries: Metal Band Saws in Action
Metal band saws find applications across numerous industries, showcasing their versatility and importance in modern manufacturing and fabrication. In the construction industry, these saws cut structural steel beams, pipes, and rebar to precise lengths for building projects. Fabrication shops rely on metal band saws for cutting raw stock into manageable pieces for further processing. The automotive industry utilizes these machines for cutting chassis components, exhaust systems, and custom parts for both production vehicles and aftermarket modifications.
Aerospace manufacturers employ high-precision band saws to cut specialized alloys used in aircraft and spacecraft construction. In the energy sector, metal band saws cut large-diameter pipes for oil and gas transportation, as well as components for wind turbines and solar panel mounting systems. Shipbuilding yards use these saws to cut thick steel plates and shape structural elements for vessel construction. The furniture industry benefits from metal band saws when working with metal frames and decorative elements.
Artists and sculptors often turn to metal band saws for cutting and shaping materials for large-scale installations and intricate metal artwork. In the realm of prototyping and research, these saws enable quick and accurate cutting of various metals for experimental designs and testing. Even in the field of dentistry, small-scale metal band saws find use in cutting precious metals for dental implants and crowns. The wide-ranging applications of metal band saws across these diverse industries underscore their importance as versatile and indispensable cutting tools.
Blade Selection: Matching the Right Blade to the Task
Selecting the appropriate blade for a metal band saw significantly impacts cutting performance and efficiency. Blade selection involves considering several factors, including the material being cut, its thickness, and the desired cut quality. Tooth pitch, measured in teeth per inch (TPI), plays a crucial role in blade selection. Coarser pitches with fewer teeth per inch suit thicker materials and provide faster cutting speeds, while finer pitches offer smoother finishes on thinner materials. Variable pitch blades, featuring alternating tooth spacing, reduce vibration and noise during cutting.
The blade’s width affects its ability to make straight cuts and tight curves, with wider blades providing more stability for straight cuts and narrower blades allowing for tighter curves. Blade materials also vary, with high-speed steel (HSS) blades offering good performance for general-purpose cutting. Bi-metal blades, combining a high-speed steel cutting edge with a flexible steel backing, provide increased durability and heat resistance.
For cutting extremely hard or abrasive materials, carbide-tipped blades offer superior wear resistance and cutting performance. The blade’s set, or the way the teeth are bent, affects the width of the cut and chip clearance. A raker set, with every third tooth bent, suits most general-purpose cutting tasks. A wavy set, with groups of teeth bent alternately, excels at cutting thin materials. Choosing the right combination of these blade characteristics ensures optimal cutting performance and extends blade life across various metalworking applications.
Maintenance and Safety: Ensuring Longevity and Operator Protection
Proper maintenance of metal band saws ensures their longevity and optimal performance, while adherence to safety protocols protects operators from potential hazards. Regular cleaning of the saw removes metal chips and debris that can interfere with smooth operation. Lubrication of moving parts, including blade guides and wheel bearings, reduces wear and maintains smooth blade tracking. Checking and adjusting blade tension before each use prevents blade wandering and potential breakage. Inspecting the blade regularly for signs of wear or damage allows for timely replacement, preventing poor cut quality and potential safety issues.
Proper blade break-in procedures, involving running new blades at reduced speeds for a period, extend blade life and improve cutting performance. Maintaining proper alignment of the blade guides and support bearings ensures straight, accurate cuts and prevents premature blade wear. Regularly checking and replacing coolant in machines with cooling systems prevents corrosion and improves cutting efficiency. On the safety front, proper training for all operators on machine operation and safety protocols is essential. Using appropriate personal protective equipment, including safety glasses, gloves, and hearing protection, safeguards operators from potential injuries.
Ensuring all safety guards are in place and functioning correctly before operating the saw prevents accidental contact with the moving blade. Implementing proper material handling techniques, including the use of material handling equipment for large or heavy workpieces, reduces the risk of injuries. Establishing clear work zones around the band saw and maintaining a clutter-free work area minimize trip hazards and allow for safe operation. Regular safety audits and equipment inspections help identify and address potential hazards before they lead to accidents. By prioritizing both maintenance and safety, metalworking facilities can ensure their metal band saws remain productive, efficient, and safe tools for years to come.
Advancements in Technology: The Future of Metal Band Saws
Technological advancements continue to enhance the capabilities and efficiency of metal band saws. Computer Numerical Control (CNC) integration allows for automated cutting sequences, improving precision and reducing operator intervention. These CNC-controlled band saws can execute complex cutting patterns and optimize material usage, significantly boosting productivity in high-volume production environments. Advanced blade materials and coatings, such as titanium nitride (TiN) and diamond-like carbon (DLC), extend blade life and enable cutting of increasingly hard and exotic materials.
Servo-driven feed systems provide precise control over cutting speed and pressure, adapting to variations in material properties for optimal cutting performance. Industry 4.0 technologies are making their way into metal band saw design, with features like remote monitoring and predictive maintenance capabilities. These smart systems can track machine performance, predict potential failures, and schedule maintenance activities, minimizing downtime and improving overall equipment effectiveness. Augmented reality (AR) applications are emerging as valuable tools for operator training and maintenance guidance, providing real-time information and step-by-step instructions overlaid on the physical machine.
Improved energy efficiency through the use of regenerative drives and optimized motor designs reduces power consumption and operating costs. Additive manufacturing techniques are being explored for producing custom band saw components, potentially leading to more efficient designs and reduced lead times for replacement parts. As these technologies continue to evolve, metal band saws are poised to become even more integral to advanced manufacturing processes, offering unprecedented levels of precision, efficiency, and automation in metalworking operations.
Choosing the Right Metal Band Saw: Factors to Consider
Selecting the appropriate metal band saw requires careful consideration of several factors to ensure it meets specific cutting needs. The type of materials to be cut plays a crucial role in the decision-making process. Different metals require varying blade speeds and tooth configurations, so choosing a saw with adjustable speed settings offers greater versatility. The thickness and size of the workpieces determine the necessary throat depth and cutting capacity of the saw. For operations involving a wide range of material sizes, a saw with adjustable blade guides provides flexibility.
The volume of work and required production speed influence the choice between manual and automatic feed systems. High-volume operations benefit from automatic feed systems that increase productivity and consistency. Available floor space in the workshop impacts the choice between vertical and horizontal band saw configurations. Vertical band saws often have a smaller footprint but may have limitations on the size of materials they can handle. The precision requirements of the cutting tasks guide the selection of features like blade tensioning systems and guide bearings.
For highly precise cuts, saws with advanced blade tensioning and guiding mechanisms offer superior performance. Budget considerations not only include the initial purchase price but also long-term factors like energy efficiency, maintenance costs, and blade longevity. Evaluating these aspects helps in choosing a saw that provides the best value over its lifetime. Additionally, considering future needs and potential expansion of cutting capabilities ensures the selected band saw remains relevant as business requirements evolve. By carefully weighing these factors, metalworking professionals can choose a metal band saw that optimally balances performance, versatility, and cost-effectiveness for their specific applications.
Conclusion: The Cutting Edge of Metalworking Excellence
Metal band saws stand as cornerstones of modern metalworking, offering unparalleled versatility and precision in cutting operations. From small workshops to large industrial facilities, these machines shape the metal components that form the foundation of countless products and structures. The diverse range of metal band saw types, each with its unique strengths, ensures that there’s a suitable option for every cutting task. Vertical band saws excel in custom fabrication, while horizontal models efficiently handle large stock and repetitive cuts.
Portable saws bring cutting power to job sites, and specialized contour saws create complex shapes with ease. The key components of metal band saws work in harmony to deliver accurate cuts, with advancements in blade technology, motor efficiency, and control systems continuously improving performance. Proper cutting techniques, combined with appropriate blade selection and regular maintenance, unlock the full potential of these machines. As metal band saws find applications across various industries, from construction and automotive to aerospace and artistry, their importance in the manufacturing landscape continues to grow.