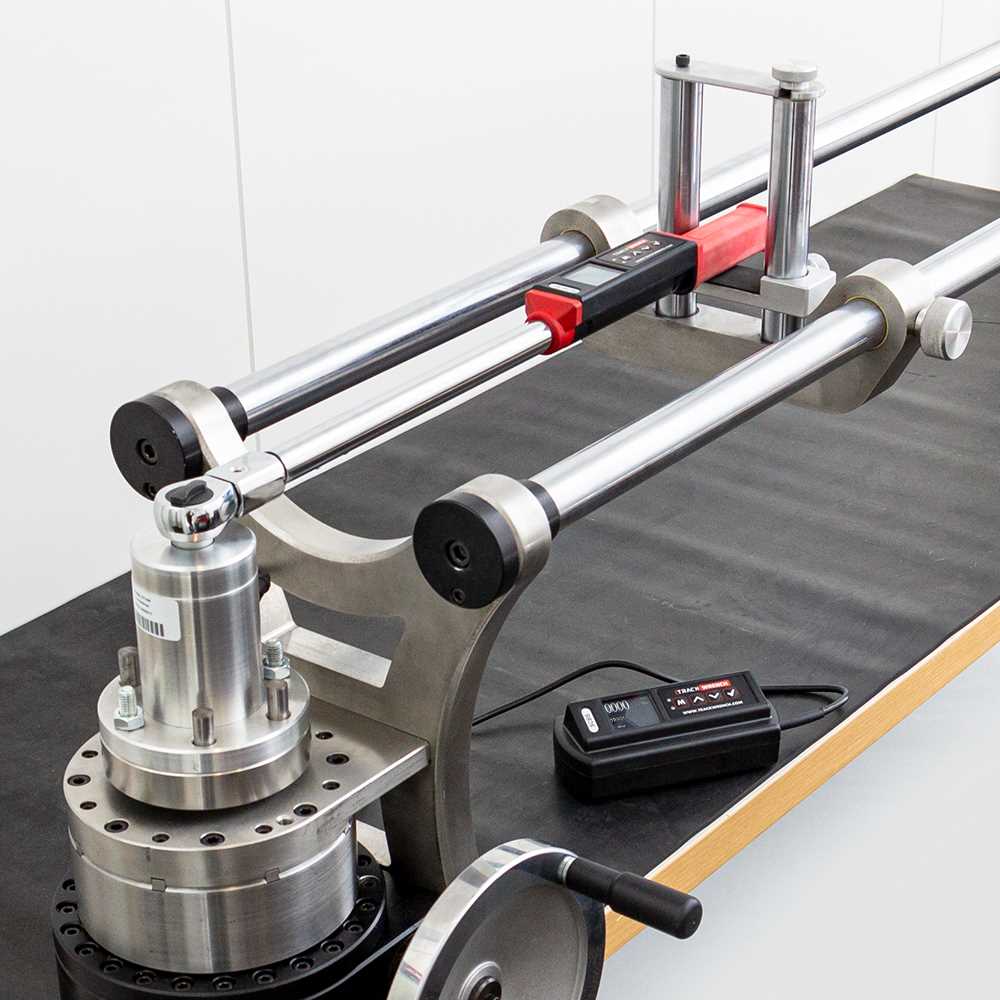
How to Perform Torque Wrench Calibration: A Step-by-Step Guide
What is Wrench Calibration?
Torque wrench calibration ensures the tool accurately measures torque applied to fasteners. Calibration verifies the wrench’s precision by comparing its readings against standard values. This process is essential for tools used in critical applications like automotive or aerospace industries.
Definition and Purpose
Torque wrench calibration is the process of testing and adjusting a wrench to meet manufacturer specifications. It ensures the torque applied to bolts or nuts is neither too low nor excessive. The purpose is to maintain tool accuracy, prevent mechanical faults, and ensure safety during operations. Accurate calibration minimizes over-tightening and under-tightening risks.
Tools Used in Calibration
Specialized tools are crucial for calibration to achieve precise results. These include torque standards, calibration benches, and torque analyzers. Torque standards check the wrench’s output against pre-defined values. Calibration benches securely hold the wrench during tests, providing stability. Torque analyzers measure and record applied force digitally, aiding adjustments and documentation. Quality tools ensure reliable calibration outcomes.
Why is Wrench Calibration Important?
Torque wrench calibration is essential for maintaining efficiency and safety across various industries. Accurate calibration ensures your torque wrench delivers precise readings and avoids costly mistakes. Regular calibration keeps operations smooth and reliable.
Ensuring Accuracy in Measurements
Calibrating a torque wrench ensures its readings match standard values. Accurate measurements prevent over-tightening or under-tightening fasteners. This accuracy is crucial in precision-driven fields like automotive, aerospace, and manufacturing. Unreliable measurements can compromise equipment performance and safety.
Preventing Equipment Damage
Improper torque application can damage fasteners or machinery. Over-tightened bolts may strip threads or crack components. Under-tightened parts can loosen, causing operational failure. Regular calibration minimizes these risks and prolongs equipment lifespan. It maintains mechanical integrity and avoids costly repairs.
Improving Safety Standards
Calibrated wrenches enhance workplace safety by ensuring secure fastener tightening. Faulty torque wrenches can lead to structural issues or accidents. Industries like construction and aviation rely on calibrated tools to meet safety requirements. Regular calibration helps create a safer environment for workers and equipment alike.
How Often Should a Torque Wrench Be Calibrated?
Regular calibration is crucial for maintaining a torque wrench’s reliability and accuracy. Different industries follow specific guidelines and schedules to ensure peak performance.
Industry Guidelines for Calibration Frequency
Torque wrench calibration frequency depends on industry standards and tool usage. Many industries, like automotive and aerospace, recommend calibrating every 12 months. High-use tools may require more frequent calibration, such as every six months. Critical safety applications often demand calibration before each significant use. Following industry guidelines helps meet safety and performance standards.
Factors Influencing Calibration Schedules
Several factors affect calibration schedules. Frequent usage can cause wear and reduce accuracy. Harsh environments, like extreme temperatures or humidity, can impact tool performance. Manufacturing defects or accidental damage may also require immediate recalibration. Monitoring these factors ensures your wrench stays accurate and reliable. Adapting schedules to usage and conditions keeps tools performing efficiently.
Methods of Wrench Calibration
Torque wrench calibration involves precise techniques to ensure accurate and reliable measurements. Two main methods are widely used: mechanical calibration and digital calibration. Both methods have specific applications and advantages.
Mechanical Calibration Methods
Mechanical calibration methods rely on traditional tools and manual techniques. These include using torque calibration devices like beam arms or calibrated weights.
- Torque Beam Arm: This measures the force applied by the wrench by comparing it to a known standard. The beam arm highlights differences for adjustment.
- Calibrated Weights: These apply a fixed load to the wrench, testing if it delivers the expected output.
Mechanical methods are cost-effective and time-tested. However, they require skilled technicians for accurate results. These techniques are ideal for basic calibration without complex machinery.
Digital Calibration Techniques
Digital calibration is a modern method using advanced electronic devices. These tools measure torque digitally with greater precision.
- Torque Analyzers: These devices digitally record applied force and compare it to preset values. They are highly accurate and efficient for repeated tests.
- Calibration Benches: These secure the wrench in place and use electronic systems to apply torque loads. They offer computerized data analysis for calibration adjustments.
Digital techniques are faster and more accurate, suitable for industries requiring stringent standards. They ensure detailed reporting and compliance with industry regulations.
Both mechanical and digital methods play vital roles in ensuring torque wrench reliability. Selecting the appropriate method depends on your operational needs and budget.
Signs Your Torque Wrench Needs Calibration
Regular calibration is essential to maintain accurate torque readings and tool performance. Miscalibrated torque wrenches can lead to inefficiency and safety risks. Recognizing the signs of miscalibration ensures timely corrective measures.
Symptoms of Miscalibration
- Incorrect Torque Readings: A miscalibrated wrench may show torque values that differ from actual applied force. This can result in improper fastening.
- Frequent Fastener Failures: Fasteners may loosen, strip, or break if the torque wrench applies incorrect force.
- Abnormal Tool Wear: Excessive or uneven wear on the wrench could indicate calibration issues.
- Unusual Sounds or Resistance: Sudden clicking sounds or resistance during operation may point to calibration problems.
- Past Calibration Expiry: Failing to calibrate within industry-recommended timelines increases the risk of reduced accuracy.
Being aware of these symptoms can help identify miscalibration early and maintain the wrench’s effectiveness.
Risks of Using an Improperly Calibrated Wrench
- Safety Hazards: Improper torque application may lead to loose fasteners, causing accidents or equipment failure.
- Damage to Equipment: Over-tightened fasteners can strip threads or crack components, reducing their lifespan.
- Costly Repairs and Downtime: Incorrect fastener torque can cause machinery breakdowns, leading to expensive repairs and lost productivity.
- Non-Compliance Issues: Industries with strict regulations, like aerospace, might face compliance challenges due to inaccurate torque tools.
- Reduced Operational Efficiency: A faulty wrench impacts productivity and compromises work quality.
Understanding these risks highlights the importance of timely calibration to ensure safe and smooth operations.
Benefits of Professional Calibration Services
Professional calibration services ensure that your torque wrench remains accurate and reliable. Leveraging expert knowledge and advanced tools, these services deliver precision and long-term benefits.
Expertise and Precision
Calibration experts use specialized equipment to achieve highly accurate results. Their training ensures proper adjustments according to manufacturer standards. This precision helps identify minor inaccuracies in torque wrench readings. By relying on professionals, you reduce the risk of errors and achieve consistent performance.
Prolonging Tool Lifespan
Regular professional calibration extends your torque wrench’s lifespan. Experts detect wear and tear early and recommend preventive actions. Addressing potential issues promptly can avoid permanent tool damage. Proper calibration also maintains the tool’s structural integrity over time. This minimizes repair costs and maximizes long-term value.
Certification and Compliance
Professional services provide detailed calibration certificates. These documents confirm that your torque wrench meets industry standards. Certification is crucial for regulated sectors like aviation, automotive, and construction. It ensures compliance with safety and quality requirements. Proper records also simplify audits and inspections when needed.
Investing in professional calibration services enhances accuracy, reduces risks, and meets regulatory demands.
DIY Calibration: Pros and Cons
DIY torque wrench calibration can be tempting for cost-saving and convenience. However, it comes with both advantages and potential risks. Understanding these helps you decide whether DIY calibration suits your needs or if professional services are a better choice.
Steps for Basic DIY Calibration
- Collect Necessary Tools: Gather a torque tester, calibration weights, and a solid workbench.
- Set a Stable Workspace: Choose a flat, well-lit area with no distractions or movement.
- Test Readings on a Torque Tester: Secure the wrench on the tester and apply force to measure torque accuracy.
- Compare with Manufacturer Standards: Match the output of the wrench with recommended values specified by its maker.
- Adjust Settings if Necessary: Use the wrench’s adjustment mechanism to correct any discrepancies.
- Retest for Accuracy: Perform multiple tests to confirm that the wrench meets precise standards.
- Document Outcomes: Record calibration results and monitoring details for future reference.
These steps can help maintain your wrench temporarily, ensuring it delivers reliable results.
Potential Pitfalls of DIY Calibration
- Lack of Specialized Equipment: DIY methods often lack precision tools used in professional calibration.
- Limited Accuracy: Minor discrepancies may go unnoticed, leading to inaccurate torque measurements.
- Time-Consuming Process: DIY calibration takes time and requires meticulous attention to detail.
- Risk of Tool Damage: Incorrect adjustments can result in permanent damage to the torque wrench.
- No Certification: Lack of proper compliance documentation may affect work in regulated industries.
While DIY calibration offers cost benefits, it may not guarantee professional-grade accuracy and compliance. Assess your requirements and proceed cautiously.
Tips for Maintaining Wrench Calibration
Regular upkeep ensures your torque wrench stays accurate and reliable. Follow these tips to maintain calibration effectively.
Proper Tool Handling and Storage
- Store in a Controlled Environment: Keep the wrench in a dry, temperature-stable space to prevent damage.
- Protect from Impact: Avoid dropping or mishandling the wrench to prevent calibration shifts.
- Handle with Care: Operate the wrench within its specified torque range to minimize wear.
- Use Protective Cases: Invest in storage cases to shield the tool from dust, moisture, or physical impacts.
- Avoid Overuse: Rotate usage across multiple tools to reduce strain on individual wrenches.
Proper handling significantly prolongs your tool’s lifespan while maintaining its accuracy.
Regular Testing and Maintenance
- Schedule Routine Inspections: Test calibration periodically based on industry recommendations or tool usage.
- Monitor Performance: Keep track of measurement discrepancies that indicate calibration issues.
- Clean Regularly: Remove dirt and grease buildup to prevent wear on mechanical components.
- Lubricate Moving Parts: Ensure smooth operation by applying lubricant where needed.
- Seek Professional Help: Have experts check calibration if abnormalities persist or official certification is required.
Consistent testing and maintenance help ensure the wrench stays dependable and precise over time.
Best Practices for Torque Wrench Users
Following best practices ensures that your torque wrench remains accurate and reliable.
Follow Manufacturer Guidelines
Always adhere to the manufacturer’s instructions for calibration and maintenance. These guidelines are tailored to your specific torque wrench model, ensuring optimal performance.
Use Correct Torque Settings
Set the torque wrench to the recommended settings for each application. Using incorrect settings can lead to over-tightening or under-tightening, compromising the assembly’s integrity.
Avoid Prolonged Loading
Do not leave the torque wrench in a fixed position after tightening. Prolonged loading can cause bending or stretching of the wrench’s components, leading to inaccurate readings.
Calibrate After Extensive Use
If your torque wrench undergoes extensive use, schedule a calibration sooner than usual. Heavy usage can accelerate wear and affect the wrench’s accuracy more quickly.
Train Proper Usage
Ensure that all users are trained in the correct operation and handling of torque wrenches. Proper usage reduces the risk of damage and maintains calibration accuracy.
The Cost of Neglecting Wrench Calibration
Ignoring regular torque wrench calibration can lead to significant costs and operational issues.
Increased Risk of Equipment Failure
Inaccurate torque application can cause equipment to fail, leading to costly repairs and potential downtime in operations.
Safety Hazards
Over-tightening can result in broken bolts or damaged components, creating safety hazards for operators and end-users. Under-tightening can lead to loose parts, risking structural integrity.
Non-Compliance Penalties
Failing to adhere to industry standards through improper calibration can result in non-compliance penalties, legal issues, and damage to your business’s reputation.
Higher Long-Term Costs
Repairing or replacing damaged equipment due to improper torque settings incurs higher long-term costs compared to the relatively low expense of regular calibration.
Frequently Asked Questions
What is torque wrench calibration?
Torque wrench calibration is the process of verifying and adjusting a torque wrench to ensure it measures torque accurately. It involves comparing the wrench’s readings with a known torque standard and making necessary adjustments.
How often should I calibrate my torque wrench?
Calibration frequency depends on usage and industry standards. Generally, calibrate annually or after significant use. However, high-usage environments may require more frequent calibration.
Can I calibrate my torque wrench myself?
Basic checks and maintenance can be performed in-house with the right tools. However, precise calibration often requires professional services to ensure accuracy and reliability.
What happens if my torque wrench is not calibrated?
An uncalibrated torque wrench can deliver inaccurate torque measurements, leading to over-tightening or under-tightening. This can cause equipment failure, safety hazards, and increased operational costs.
Where can I get my torque wrench calibrated?
Professional calibration services are available through specialized calibration labs, some tool suppliers, and equipment service centers. Ensure the provider is certified and accredited for accurate results.
Conclusion
Torque wrench calibration is essential for maintaining the accuracy, reliability, and safety of your fastening applications. By understanding the importance of calibration, following a regular maintenance schedule, and selecting reputable calibration services, you ensure that your torque wrenches perform optimally. Whether in automotive repair, aerospace, or industrial settings, precise torque application is critical. Embrace the practice of regular calibration, and experience the benefits of enhanced performance, safety, and cost-efficiency in your operations.