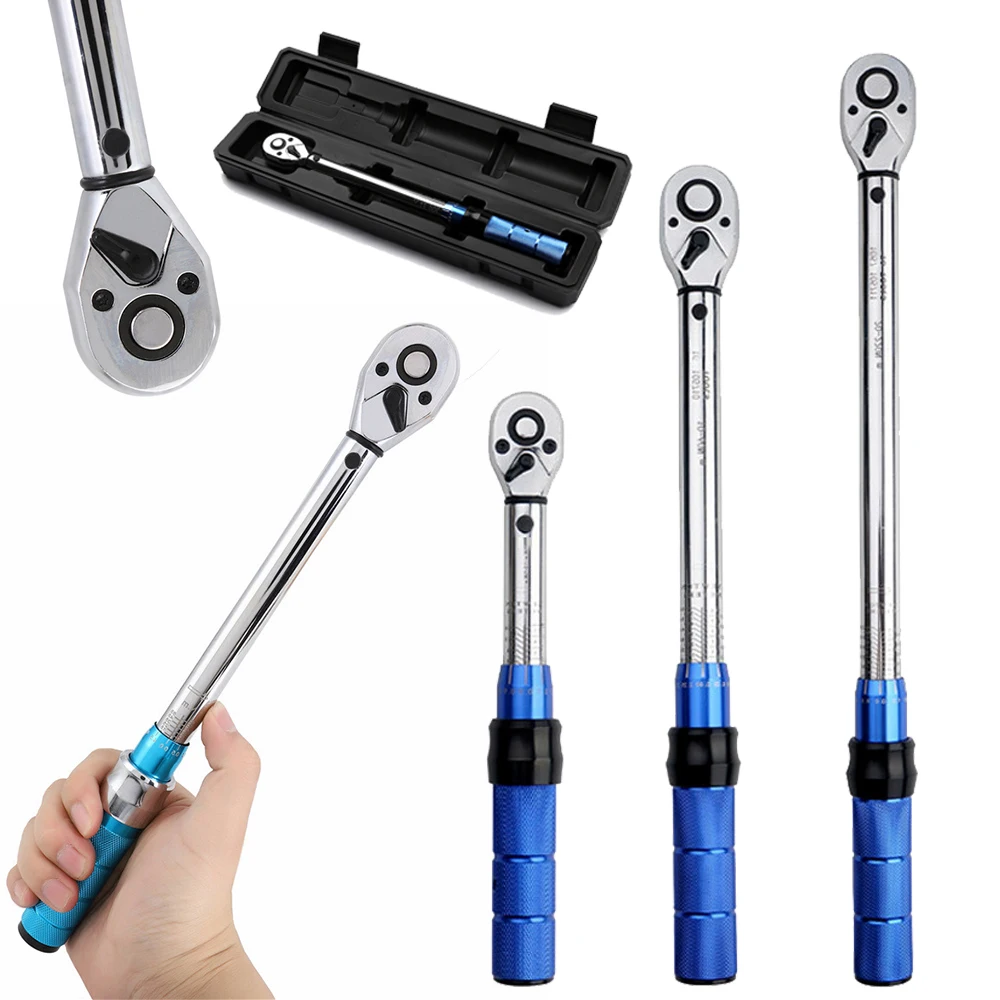
How to Use Torque Wrench Correctly for Optimal Tightening
A torque wrench allows you to tighten bolts and nuts to the manufacturer’s specifications, preventing over-tightening or under-tightening, which can lead to equipment failure or safety hazards. Whether you’re a seasoned mechanic or a hobbyist, understanding the proper use of a torque wrench can significantly enhance the quality and reliability of your work. This comprehensive guide will walk you through everything you need to know about how to use torque wrench.
Understanding the Torque Wrenches
Types of Torque Wrenches
There are several types of torque wrenches, each suited for different applications. Understanding these variations helps in selecting the right tool for your needs.
Beam Torque Wrenches
The beam torque wrench is the most basic type. It features a simple design where a beam deflects under torque. The user reads the torque value through a scale as the beam moves.
Click Torque Wrenches
The click torque wrench is the most commonly used type. It emits a distinct click sound when the set torque level is reached, signaling the user to stop applying force. This feature prevents over-tightening and ensures accurate torque application.
Digital Torque Wrenches
Digital torque wrenches offer precise readings on a digital display. They often include features like memory storage, programmable settings, and audible alerts, making them highly accurate and user-friendly.
Dial Torque Wrenches
Dial torque wrenches use a dial gauge to display torque values. They provide precise measurements and are favored for high-torque applications where accuracy is paramount.
Choosing the Right Torque Wrenches
Selecting the appropriate torque wrench is the first step in mastering how to use torque wrenches. Factors to consider include the type of projects you’re working on, the torque range required, and the accuracy needed.
Determining Torque Range
Identify the torque range your projects require. For automotive work, torque wrenches typically range from 10 Nm to 300 Nm. Ensure the wrench you choose covers this range to handle various tasks.
Accuracy and Calibration
Accuracy is vital for ensuring bolts are tightened correctly. Look for torque wrenches with an accuracy of ±4% or better. Regular calibration is necessary to maintain precision over time.
Handle Length and Comfort
A longer handle provides better leverage, making it easier to apply the desired torque. Additionally, ergonomic designs enhance comfort during prolonged use, reducing fatigue and improving control.
Material and Durability
Choose torque wrenches made from high-quality materials like chrome vanadium steel. Durable construction ensures longevity and reliable performance, even in demanding environments.
How to Use a Torque Wrench Correctly
Knowing how to use torque wrench correctly involves understanding the proper technique, calibration, and maintenance. Follow these essential steps to ensure accurate and safe torque application.
Step 1: Read the Manufacturer’s Instructions
Always start by reading the manufacturer’s instructions specific to your torque wrenches model. Different types have unique features and operational guidelines that must be followed for optimal performance.
Step 2: Set the Desired Torque
Adjust the torque setting to the specified value required for your project. For click and dial torque wrenches, turn the handle until the desired torque reading is achieved. For digital wrenches, input the torque value using the digital interface.
Step 3: Select the Appropriate Socket
Choose a socket that fits the bolt or nut you’re working on. A mismatched socket can cause improper torque application or damage the fastener. Ensure the socket is securely attached to the torque wrenches.
Step 4: Apply Force Gradually
Place the socket onto the fastener and begin applying force gradually. For click and dial wrenches, listen for the click sound or watch the dial indicator as you tighten. Stop applying force once the set torque is reached.
Step 5: Maintain Consistent Pressure
Apply even pressure throughout the tightening process. Avoid sudden jerks or uneven force, as these can lead to inaccurate torque readings and potential damage.
Step 6: Release the torque wrenches Properly
After applying the torque, release the wrench according to the manufacturer’s instructions. For click and dial wrenches, reset the handle to the lowest setting to prevent strain on the mechanism.
Best Practices for Using a Torque Wrench
Implementing best practices when using a torque wrench enhances accuracy and extends the tool’s lifespan. Here are some key practices to follow:
Use the Correct Tool for the Job
Different jobs require different types of torque wrenches. Ensure you’re using the appropriate wrench type that matches the torque range and application requirements.
Maintain Proper Calibration
Regular calibration is crucial for maintaining the accuracy of your torque wrenches. Follow the manufacturer’s recommendations for calibration frequency, typically annually or after a specific number of uses.
Store Properly
Store your torque wrenches in a dry, clean environment. Avoid exposure to moisture and extreme temperatures, which can affect the tool’s precision and longevity. Use a protective case or sleeve to prevent damage when not in use.
Avoid Over-Torquing
Applying excessive torque can strip threads, damage fasteners, and reduce the effectiveness of your torque wrenches. Always adhere to the recommended torque specifications provided by the manufacturer or project guidelines.
Use Extension Bars Sparingly
While extension bars can provide additional leverage, they can also introduce inaccuracies in torque application. Use them only when necessary and ensure they are securely attached to minimize the risk of slippage or miscalculation.
Practice Proper Technique
Developing a consistent tightening technique improves reliability and accuracy. Practice smooth, steady movements and avoid abrupt force applications that can skew torque readings.
Common Mistakes to Avoid When Using a Torque Wrench
Understanding and avoiding common mistakes is essential for mastering how to use torque wrench effectively. Here are some frequent errors and how to prevent them:
Using the Wrong Torque Wrenches Type
Using an incorrect torque wrench type for a specific task can lead to inaccurate readings and potential damage. Always choose a wrench that matches the torque range and application needs of your project.
Skipping Calibration
Neglecting regular calibration can result in drift and inaccurate torque measurements. Make calibration a routine part of your maintenance schedule to ensure ongoing precision.
Over-Reliance on Audible or Visual Cues
Relying solely on the click sound or dial indicator can sometimes be misleading if the wrench is not properly calibrated. Cross-check torque readings with additional measurements or use multiple torque references when necessary.
Applying Torque in Multiple Directions
Applying torque in a single direction ensures consistent tightening. Avoid twisting the wrench in multiple directions, which can affect the accuracy and effectiveness of the torque application.
Neglecting to Reset the Torque Setting
After use, always reset the torque wrenches to its lowest setting. Leaving it set at a high torque value can cause unnecessary strain on the wrench and lead to inaccurate measurements in future uses.
Maintaining Your Torque Wrenches
Proper maintenance is vital for ensuring the longevity and reliability of your torque wrenches. Follow these maintenance tips to keep your tool in top condition:
Clean Regularly
After each use, wipe down the torque wrenches with a clean, dry cloth to remove dirt, grease, and moisture. This prevents corrosion and keeps the mechanism smooth.
Lubricate Moving Parts
Periodically lubricate the wrench’s moving parts with a light machine oil. This ensures smooth operation and prevents rusting of internal components.
Inspect for Damage
Regularly inspect your torque wrenches for any signs of wear or damage. Look for cracks, loose parts, or any irregularities that could compromise its accuracy and functionality.
Store in a Protective Case
When not in use, store your torque wrenches in its protective case to shield it from dust, moisture, and physical damage. This also helps maintain its calibration and overall condition.
Follow Manufacturer’s Guidelines
Adhere to the maintenance guidelines provided by the manufacturer. These instructions are tailored to your specific torque wrenches model and ensure optimal performance and longevity.
Advanced Techniques for Using a Torque Wrench
For those looking to take their skills to the next level, mastering advanced techniques can enhance the effectiveness and versatility of your torque wrenches.
Incremental Tightening
In scenarios where multiple fasteners need to be tightened, apply torque incrementally. This ensures even distribution of force and prevents uneven tightening, which can lead to gaps or misalignment.
Dynamic Tightening
Dynamic tightening involves tightening the fastener in a pattern, such as a star or crisscross sequence. This technique is particularly useful for components like wheels or engine parts, where balanced torque distribution is crucial.
Using Manufacturer-Specific Torque Values
Always refer to the manufacturer’s torque specifications for your specific motorcycle or equipment. Different components and brands may have unique torque requirements that must be adhered to for optimal performance and safety.
Combining with Other Tools
Integrate your torque wrenches with other specialized tools, such as impact drivers or ratchets, to improve efficiency and accuracy in complex projects. Ensure compatibility and proper usage to maintain torque wrenches precision.
Practicing with Different Settings
Experiment with various torque settings on scrap materials to become familiar with the wrench’s response and behavior. This hands-on practice enhances your ability to predict and control torque application in real-world scenarios.
Safety Tips When Using a Torque Wrench
Safety should always be a priority when using a torque wrench. Follow these safety tips to prevent accidents and ensure a secure working environment:
Wear Protective Gear
Always wear appropriate protective gear, such as gloves and safety glasses, to protect yourself from potential injuries and debris during the tightening process.
Secure the Workpiece
Ensure that the motorcycle or equipment you’re working on is securely positioned
Troubleshooting Common Issues with Torque Wrenches
Even the best-maintained torque wrenches can encounter issues occasionally. Knowing how to use torque wrench effectively includes troubleshooting common problems to ensure continued accuracy and functionality.
Wrench Not Clicking or Beeping
If your torque wrench isn’t clicking or beeping at the set torque, first check the calibration. An out-of-calibration wrench may fail to signal correctly.
Inaccurate Readings
Inaccurate torque readings can result from several factors. Check for any visible damage to the wrench and ensure that different components, such as the handle and head, are securely attached. Recalibrate the wrench if needed and verify that it is on a flat, stable surface when taking measurements.
Over-Torquing
Sometimes, users may apply too much force even after the first cue. To prevent over-torquing, stop applying force immediately once the click or beep occurs. Additionally, practicing proper technique and using a light grip can help maintain control over the torque application.
Difficulty in Switching Settings
If you struggle to switch torque settings, inspect the knob or handle for any obstructions or damage. Lubricating the adjustment mechanism can also facilitate smoother transitions. If the problem persists, consider professional maintenance or replacement.
Wrist Strain or Fatigue
Using a torque wrench for extended periods can cause wrist strain or fatigue. To alleviate this, take regular breaks and use proper hand positioning. Using a wrench with an ergonomic handle can also reduce the physical strain during use.
Frequently Asked Questions About How to Use Torque Wrenches
Can I Use a Torque Wrench for All Fasteners?
While a torque wrench is versatile, it’s essential to use it for fasteners that require precise torque specifications. Overusing it on fasteners that don’t need exact torque can wear out the tool prematurely. Reserve the torque wrench for critical applications like engine components, wheels, and structural connections.
How Often Should I Calibrate My Torque Wrench?
Regular calibration is crucial for maintaining accuracy. It’s recommended to calibrate your torque wrench annually or after a significant drop in performance. If you frequently use your torque wrench, consider more frequent calibrations to ensure consistent precision.
What Should I Do If My Torque Wrench Is Damaged?
If your torque wrench is damaged, stop using it immediately to prevent further issues. Assess the extent of the damage and consider professional repair services if possible. In cases of severe damage, replacing the torque wrench is the safest option to maintain accurate torque application.
Is It Necessary to Reset the Torque Wrench After Use?
Yes, resetting the torque wrench to its lowest setting after use is essential. This practice helps prevent strain on the internal mechanism and maintains the tool’s accuracy. Leaving the wrench set at a high torque value can lead to premature wear and calibration drift.
Can I Use My Torque Wrench on Different Types of Fasteners?
Yes, you can use your torque wrench on various types of fasteners, provided the socket size matches the fastener head. Always select the appropriate socket to ensure proper torque application and avoid damaging the fastener or the wrench.
Conclusion
Mastering how to use torque wrench is fundamental for ensuring the integrity and safety of your mechanical projects. By understanding the different types of torque wrenches, choosing the right one for your needs, and following best practices for usage and maintenance, you can achieve precise and reliable torque measurements every time. Whether you’re tightening bolts on your motorcycle, assembling machinery, or engaging in DIY projects, the torque wrench is an indispensable tool that enhances your workmanship and ensures optimal performance. Embrace the knowledge and techniques outlined in this guide to fully leverage the benefits of using a torque wrench, and elevate the quality and safety of your endeavors.