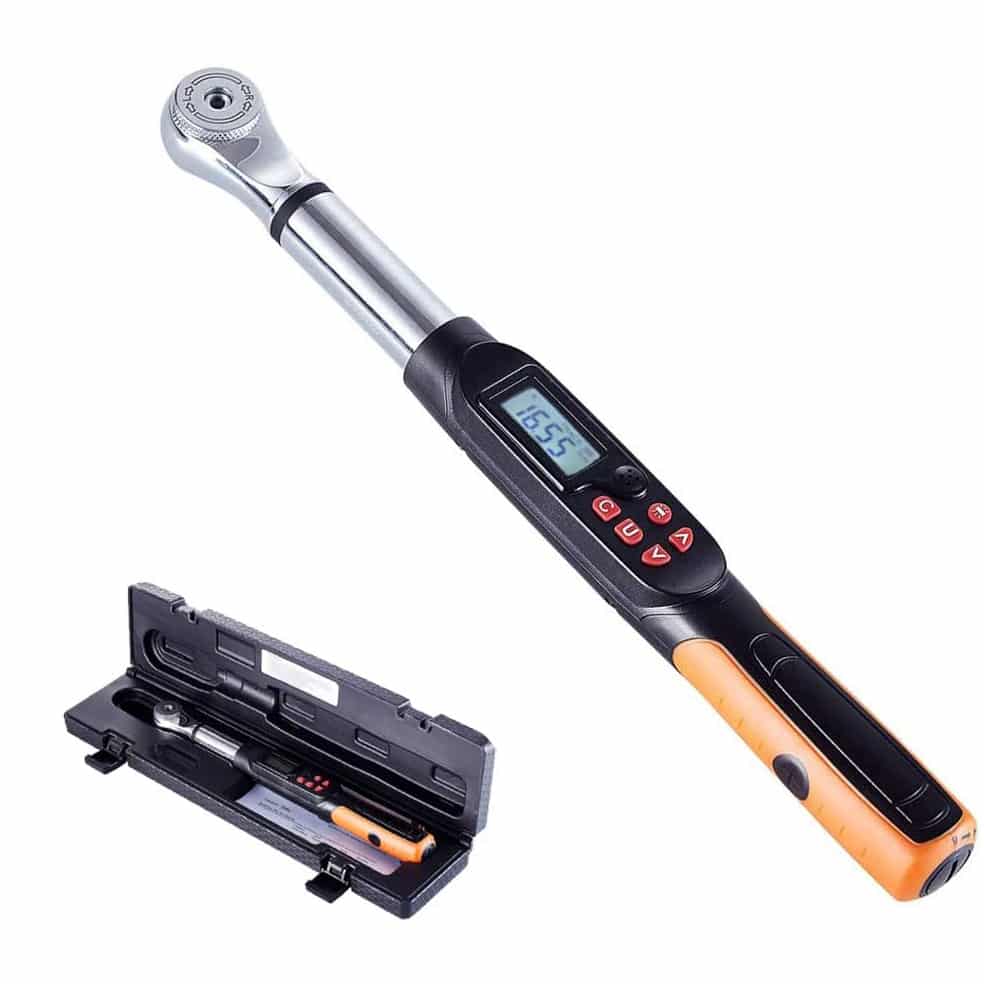
Precision Tightening: Mastering Digital Torque Wrenches
In the realm of mechanical work and precision engineering, the digital torque wrench has emerged as an indispensable tool. Combining accuracy with user-friendly features, digital torque wrenches offer unparalleled control and reliability for both professionals and DIY enthusiasts. This comprehensive guide delves into the intricacies of digital torque wrenches, exploring their benefits, functionalities, applications, and tips for selecting the perfect model to meet your needs. Whether you’re tightening bolts on a vehicle or assembling intricate machinery, understanding the capabilities of a digital torque wrench can significantly enhance your work quality and efficiency.
What is a Digital Torque Wrench
A digital torque wrench is a modern tool for precision fastening. Unlike traditional wrenches, it features an electronic display. The display shows torque value in real-time. Users set the desired torque on the tool before starting a task. It alerts the user when they reach the selected torque. This reduces the risk of over-tightening or under-tightening.
This kind of wrench is useful in industries where exact torque is critical. Examples include automotive, aerospace, and manufacturing. It assures consistency and quality in bolted connections. Digital torque wrenches offer more features than mechanical ones. For instance, they can store torque readings, which is helpful for quality control. They bring precision and accuracy to any task requiring threaded fasteners.
Digital torque wrenches cater to users looking for efficiency and precision. They fit well in both professional and hobbyist settings. They are user-friendly with easy-to-read displays and ergonomic designs. Overall, digital torque wrenches represent a leap forward in fastening technology.
How Digital Torque Wrenches Work
Digital torque wrenches operate using strain gauge technology, which detects the deformation of the wrench’s head when torque is applied. This data is then processed by an internal microchip, converting the mechanical force into an electronic signal. The digital display presents the torque value in real-time, allowing users to monitor and adjust their tightening precisely. Additionally, many digital torque wrenches come with built-in memory, sound alerts, and data logging capabilities, enhancing their functionality and user experience.
Benefits of Using a Digital Wrench
Choosing a digital torque wrench can significantly enhance the fastening process. Here are several compelling benefits:
- Increased Accuracy: Digital torque wrenches offer precise torque readings. This precision helps in achieving the correct level of tightness every time.
- Consistency in Fastening: These tools ensure consistent torque application across multiple fastenings. This is crucial in many industrial settings.
- Data Recording: The ability to record and store torque values aids in quality control. Users can reference these recordings for future analysis.
- User Notifications: The wrench alerts users when they reach the set torque value. This minimizes the risk of over or under-tightening.
- Reduced Risk of Damage: By controlling the torque applied, these wrenches help prevent damage to materials or fasteners.
- Enhanced Productivity: With quick settings and easy-to-read displays, users work more efficiently.
- Ergonomic Advantages: Digital torque wrenches are designed with the user’s comfort in mind. They often feature ergonomic grips and designs to reduce strain.
Adopting a digital torque wrench can lead to better outcomes in any precision fastening task. It is an investment in quality, efficiency, and reliability. Whether for professional or hobbyist use, the advantages are clear and impactful.
How Digital Wrenches Work
Digital torque wrenches revolutionize fastening with their advanced mechanics. At their core, they measure torque using electronic sensors. These sensors relay information to a digital display, informing the user in real time. The operation is straightforward. First, you input the desired torque level using the digital interface. As you apply force, the wrench’s sensors detect the torque and show it on the display.
When the preset torque is reached, the wrench signals the user. This alert can be a beep, vibration, or visual cue on the display. It tells you to stop applying force. This feature prevents over-tightening and ensures precision. The integrated memory function can save torque readings. This is helpful for tracking and quality control across multiple fastenings.
Every digital torque wrench comes with a calibration certificate. This ensures that the readings you get adhere to industry standards. It is vital for tasks where exact torque specifications are critical. The use of a digital torque wrench simplifies the fastening process. It brings accuracy, efficiency, and reliability to jobs where these traits are non-negotiable.
Key Features to Look for in a Digital Wrench
When choosing a digital torque wrench, consider these key features for the best performance:
- Adjustable Torque Settings: Flexibility in setting torque values is crucial. Look for wrenches that offer a wide range of settings.
- Accuracy and Precision: High precision is non-negotiable. Select wrenches with a reputation for accurate readings.
- Memory Function: Choose wrenches that can store readings. This aids in tracking and quality control.
- Durability: Ensure the wrench is robust and can withstand regular use. It should be made from high-quality materials.
- Calibration Alerts: Some wrenches remind you when recalibration is due. This maintains their accuracy over time.
- Comfortable Grip: A wrench with an ergonomic design will reduce hand strain. This makes it easier to use for long periods.
- Clear Display: The display should be easy to read. This prevents reading errors, even in poor lighting.
- Battery Life: Longer battery life means less downtime. Look for wrenches that stay charged through many uses.
- Alert Mechanisms: Good wrenches warn you when you hit the set torque. They may beep, vibrate, or flash.
By keeping these features in mind, you can select a digital torque wrench that meets your needs. A well-chosen wrench can enhance precision and efficiency in your projects.
Digital vs. Mechanical Torque Wrenches: A Comparison
When comparing digital vs. mechanical torque wrenches, several key differences stand out. Digital torque wrenches offer advanced features that are not present in their mechanical counterparts. Let’s look at the main aspects that set them apart.
- Real-Time Feedback: A digital torque wrench provides real-time torque readings on its display. Mechanical wrenches do not have this feature.
- Accuracy and Precision: Digital wrenches are known for high precision. Mechanical wrenches may lack the same exactness.
- Data Recording: The ability to record and store torque values is unique to digital models. This is useful for quality assurance.
- Alerts for Torque Level: Digital wrenches notify users when the set torque is reached. Mechanical wrenches rely on feel or manual gauges.
- Ease of Use: With clearer displays and ergonomic designs, digital wrenches are more user-friendly.
- Calibration: Digital wrenches often come with calibration certificates. Mechanical wrenches need manual checking and adjustment.
Digital torque wrenches are more suitable for jobs requiring precise torque specification. They provide users with features that enhance accuracy and consistency. Mechanical wrenches still serve well for general tasks where exact torque is less critical. Each type of wrench has its place in toolkits, but the digital ones shine for precision tasks.
Calibration and Maintenance of Digital Wrenches
Maintaining your digital torque wrench is crucial for its performance and longevity. Here’s a guide to keeping your wrench in top condition:
- Regular Calibration: Ensure the wrench’s accuracy by recalibrating regularly. Most manufacturers recommend calibration after 5,000 cycles or one year.
- Storage: Keep the wrench in a protective case when not in use. This prevents damage and maintains calibration.
- Cleanliness: Wipe the wrench with a clean, dry cloth after use. Avoid harsh chemicals that can damage electronic components.
- Battery Care: Replace batteries as needed. Low power can affect wrench performance and accuracy.
- Check for Wear: Inspect the wrench for signs of wear. Look for damages to the drive mechanism and the display.
- Professional Repair: If your wrench is damaged, seek professional repair. Do not attempt to fix it yourself as this could void the warranty.
Following these maintenance tips will help ensure your digital torque wrench continues to provide precise measurements and reliable service.
Common Applications and Settings Where Digital Wrenches Excel
Digital torque wrenches are invaluable in settings requiring exact torque application. Here are common uses:
- Automotive Industry: Mechanics set precise torque to secure wheels and engine parts. This ensures safety and performance.
- Aerospace: Aircraft fastenings must withstand extreme conditions. Digital wrenches provide the needed precision.
- Manufacturing: Assembly lines use them for uniform torque in mass production. This maintains product consistency.
- Electronics: Tightening components without damaging delicate circuitry is crucial. The accuracy of these wrenches is vital.
- Construction: Ensuring structural integrity requires the correct torque. Digital wrenches help prevent under or over-tightening.
- Cycling: High-end bicycles benefit from precise adjustments. It affects the ride quality and component lifespan.
In each application, the goal is to ensure optimum fastening. Digital torque wrenches excel because they combine precision with ease of use. Their data recording capabilities are also critical for maintaining quality standards.
Best Practices for Using Digital Wrenches
Proper use of digital torque wrenches is essential for getting the best results. Here’s how to maximize their potential:
- Read the Manual: Always start by reading the manual. It will guide you on the tool’s specifics.
- Pre-Use Inspection: Before use, check the wrench. Ensure it’s in good condition and calibrated.
- Set Correct Torque: Enter the precise torque needed for your task. Double-check settings to avoid errors.
- Hold Wrench Properly: Grip the wrench as directed. Maintain a steady hold to apply torque accurately.
- Apply Smooth Force: Increase force in a controlled manner. Avoid jerky movements that can skew the reading.
- Heed Alerts: When you reach the set torque, the wrench will notify you. Stop applying force immediately.
- Record Data: If your wrench stores data, save it for quality control.
- After-Use Care: After using, wipe the wrench clean and store it properly. This keeps it ready for next time.
- Stay Informed: Keep up with your wrench’s model updates and maintenance needs.
By following these best practices, your digital torque wrench will deliver accurate and reliable results with every use. Daily tasks will benefit from the precision and efficiency that digital torque wrenches bring to the table. Remember, consistency in care and use is key to maintaining the wrench’s longevity.
Future Trends in Digital Wrenches
Integration with Smart Technology
The future of digital torque wrenches lies in their integration with smart technology. Features such as Bluetooth connectivity, smartphone apps, and wireless data transfer are becoming increasingly common, allowing users to monitor and control their torque wrenches remotely. This integration enhances convenience, data management, and overall user experience.
Enhanced User Interfaces
Advancements in user interface design are making digital torque wrenches more intuitive and easier to use. Touchscreen displays, customizable settings, and user-friendly menus are improving the accessibility and functionality of these tools, catering to both novice users and seasoned professionals.
Increased Durability and Resilience
Future digital torque wrenches are expected to feature even greater durability and resilience, with advancements in materials and construction techniques. Enhanced resistance to environmental factors such as moisture, dust, and extreme temperatures will ensure that digital torque wrenches can withstand the toughest conditions and continue to deliver precise measurements.
Expanded Measurement Capabilities
As technology evolves, digital torque wrenches are likely to offer expanded measurement capabilities, including dynamic torque monitoring, multi-zone calibration, and advanced data analytics. These enhancements will provide users with more detailed insights and control, further elevating the precision and functionality of torque wrenches.
Sustainability and Eco-Friendly Designs
Sustainability is becoming a key consideration in tool design, and digital torque wrenches are no exception. Manufacturers are focusing on eco-friendly materials, energy-efficient displays, and recyclable components to reduce the environmental impact of their products. Sustainable designs not only benefit the planet but also appeal to environmentally conscious consumers.
Conclusion: Elevate Your Work with a Digital Wrench
Investing in a digital torque wrench is a strategic decision that can greatly enhance the precision, efficiency, and quality of your work. Whether you’re a professional mechanic, an industrial engineer, or a dedicated DIY enthusiast, the advanced features and superior accuracy of digital torque wrenches provide invaluable support in a wide array of applications. By understanding the benefits, functionalities, and maintenance practices associated with digital torque wrenches, you can make informed decisions and maximize the potential of this essential tool. Embrace the technological advancements and precision offered by digital torque wrenches, and elevate your work to new heights of excellence and reliability.