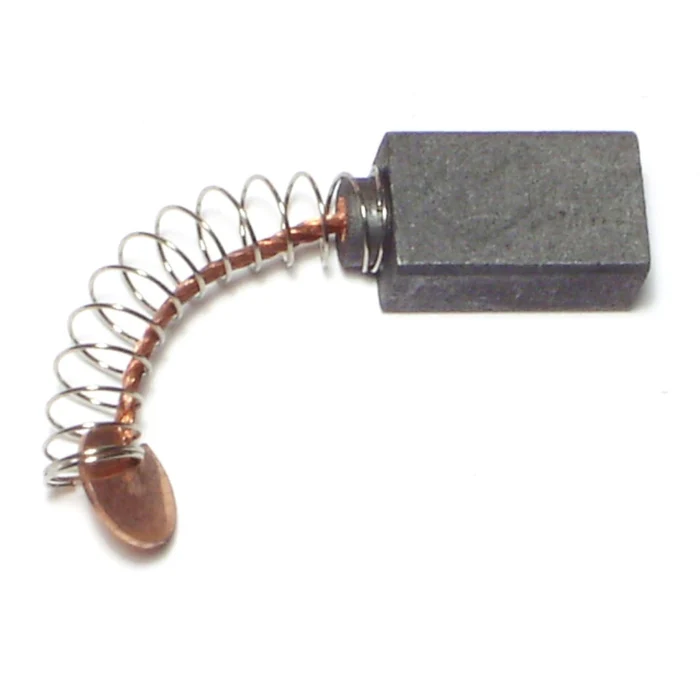
Carbon Brush: The Unsung Heroes of Electrical Machinery
Understanding Carbon Brushes
Carbon brushes are essential components used in electric motors, generators, and many other electrical devices. They play a critical role in facilitating the transfer of electrical current between stationary and rotating parts. Without carbon brushes, many machines would simply fail to operate. This blog delves deeply into the function, types, maintenance, and future of carbon brush(カーボンブラシ).
What Are Carbon Brushes?
Carbon brushes are small components made primarily from carbon or a mix of carbon and other materials. They are designed to conduct electricity between moving parts, typically a rotating shaft, and a stationary part like a commutator or slip ring. This electrical connection ensures the proper functioning of motors and generators. The choice of materials and design determines their lifespan and efficiency.
In most applications, the brushes are spring-loaded. This mechanism maintains constant contact with the rotor or commutator. As the motor operates, the brushes wear down. Consequently, regular maintenance is required to replace worn brushes. Failure to change them can lead to performance issues or even catastrophic machine failure.
Manufacturers often emphasize the importance of selecting the right carbon brush for specific applications. Various types are available, each designed for different electrical and mechanical environments. Selecting the proper carbon brush can optimize performance, longevity, and efficiency.
The Function of Carbon Brushes
Carbon brushes serve as conduits for electrical current. Their primary role is to transfer energy from a stationary component to a rotating one. This transfer occurs in various types of machinery, such as electric motors and generators. The material used to make these brushes is often graphite, which possesses excellent electrical conductivity.
Moreover, the design of carbon brushes allows them to tolerate high levels of friction and wear. This characteristic is crucial because, during operation, carbon brushes make contact with rotating parts. As they wear down, the brushes must maintain a constant electrical connection. Thus, manufacturers design brushes to ensure longevity and efficiency.
Additionally, carbon brushes help to maintain a clean electrical connection. The high conductivity of graphite minimizes energy loss. This efficiency is vital for applications where power levels need to be carefully controlled. Therefore, maintaining these components is crucial for optimal machine performance.
Transitioning to various applications, carbon brushes can be found in a wide range of equipment. From household appliances to industrial machinery, these brushes are prevalent. They ensure the seamless operation of tools like drills, lathes, and various motor-driven devices. Their presence is almost ubiquitous in the modern technological landscape.
Types of Carbon Brushes
There are different types of carbon brushes designed for specific applications. Each type has unique characteristics suited for various machinery and environmental conditions. The most common forms include those made of graphite, electrographite, and metal-graphite composites.
Graphite brushes are the most traditional. They are known for their excellent conductivity and ability to withstand thermal extremes. Because of these properties, they are widely used in general electric motors. Such brushes perform well in many standard applications.
Electrographite brushes possess a higher density and strength. They are ideal for heavy-duty applications that require high performance. These brushes can handle more wear and tear and are often used in industrial settings.
Metal-graphite brushes combine the properties of metal and graphite. This hybrid design allows for enhanced conductivity and reduced wear. They perform exceptionally well in high-speed applications. Understanding these differences can help users select the right brush for their needs.
Importance of Maintenance
Maintaining carbon brushes is crucial for ensuring optimal performance in electric machines. Regular maintenance can prevent unnecessary downtime and prolong the lifespan of both the brushes and the equipment. Neglecting this maintenance can lead to performance issues, including overheating and electrical failures.
First, monitoring the wear of carbon brushes is essential. As brushes wear down, they reduce the efficiency of electrical transfer. Regular inspections can help identify any signs of damage or excessive wear. When issues arise, timely replacement saves money in the long run.
Cleaning the brush assembly is also vital. Dust, debris, and other contaminants can accumulate over time. These substances can interrupt the electrical connection and cause malfunctions. Keeping the environment clean helps ensure the brushes work as intended.
Additionally, ensuring proper alignment is significant. Brushes must make good contact with rotating parts. Misalignment can lead to uneven wear. This unevenness decreases efficiency and can cause further operational problems.
Finally, consulting the manufacturer’s guidelines can provide tailored maintenance advice. These guidelines offer insights into specific machine requirements. Following them can help maintain the efficiency and performance of carbon brushes.
Signs of Wear and Tear
Noticing signs of wear and tear in carbon brushes is imperative for ensuring efficient machine operation. Recognizing these signs early can prevent larger, more costly issues in the future. There are several indicators that something may be wrong with your carbon brushes.
Firstly, decreased performance can signal an issue. If machines are operating below their usual efficiency, it might be due to worn brushes. Monitoring the performance levels regularly can help identify this problem.
Secondly, unusual noises during operation may point to a carbon brush problem. Grinding, buzzing, or high-pitched sounds can indicate that brushes are not making proper contact. These noises are often an early warning sign.
Visible damage is another clear indicator. If brushes appear cracked or chipped, they likely need replacement. Physical inspection allows for the identification of wear before it becomes critical.
Finally, unexpected electrical failures can stem from worn or damaged brushes. If devices suddenly stop working, checking the brushes can sometimes reveal the issue. Regular inspections and prompt replacements can help mitigate these failures.
The Benefits of Upgrading Carbon Brushes
Upgrading carbon brush offers multiple benefits. Newer materials and designs can improve performance and efficiency. Advanced options are available for various applications, making upgrades a worthwhile investment.
One major benefit is enhanced conductivity. Modern carbon brushes often incorporate advanced materials. These materials allow for better energy transfer, which enhances overall machine efficiency. This improvement can lead to significant energy savings over time.
Furthermore, upgraded brushes can offer increased lifespan. New materials resist wear and tear more effectively than older versions. This increased durability translates into reduced maintenance costs. Regular replacements can become less frequent, saving both time and money.
Reduced noise levels are also a notable advantage. Some updated designs focus on minimizing operational noise. Quieter machines lead to improved work environments, further enhancing productivity.
Finally, newer carbon brush can offer better performance under extreme conditions. For applications involving high speeds or temperatures, upgraded brushes can maintain effectiveness. This reliability can be critical for industries that demand top performance consistently.
Challenges Facing Carbon Brush Users
Despite their advantages, carbon brushes face several challenges. One primary issue is wear rate. Under harsh conditions, brushes can wear out faster than anticipated. This rapid degradation can lead to unexpected machine downtime.
Another challenge is the variability in quality among carbon brushes. Not all brushes are created equal. Low-quality brushes can significantly impact performance. Users must be diligent when selecting suppliers to ensure quality products.
Heat buildup remains another concern. Excessive heat can lead to premature failure of carbon brushes. It’s essential to implement proper cooling methods where necessary to mitigate this concern.
Lastly, users often face challenges related to sourcing and availability. Global supply chain issues can impact the availability of specific brush types. Businesses may need to consider alternative suppliers or materials in such scenarios.
The Future of Carbon Brushes
The future of carbon brushes is evolving rapidly. Innovations in materials and designs are influencing how these components function. As technology progresses, the demands for more efficient and reliable brushes become increasingly pronounced.
One exciting trend involves the use of advanced composites. These materials promise improved performance while minimizing weight. Lightweight components can enhance the overall efficiency of machinery, especially for portable devices.
Additionally, the integration of smart technology is gaining traction. Sensors that monitor brush performance can provide real-time data. Such information helps users identify when replacements are necessary before problems arise. This proactive approach may revolutionize how maintenance is conducted.
Moreover, the environmental aspect cannot be overlooked. The push for sustainability is influencing the production of carbon brushes. Manufacturers are developing eco-friendly materials that do not compromise performance. Greener options are becoming more prevalent, aligning with global sustainability goals.
Lastly, future research may lead to fully self-sustaining systems. Imagine carbon brushes designed to monitor their condition, and even self-repair. Such developments could drastically change the landscape of maintenance and component longevity.
Conclusion
In summary, carbon brushes are integral components of many electrical devices. Understanding their functionality, types, and maintenance is crucial for optimal performance. Recognizing signs of wear, considering upgrades, and looking towards future innovations are necessary steps in ensuring efficient operation.
The evolution of carbon brushes continues at a rapid pace. Keeping up with the latest advancements ensures that machines are running smoothly and efficiently. Whether through upgraded materials or smart technology, the future looks promising for this essential part.
Overall, carbon brushes remain vital in the world of electrical machinery. Their importance cannot be overstated, and diligent attention towards maintenance and upgrades will benefit numerous industries. Emphasizing these components leads to improved efficiency, reduced costs, and better overall performance.