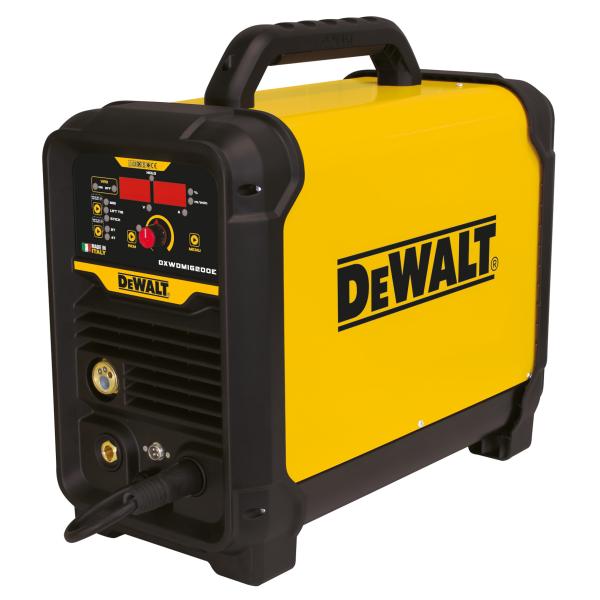
The Essential Guide to Welding Machine
The Essential Guide to Welding Machines
Welding machines are crucial tools in various industries. They bring metals together securely and efficiently. For anyone involved in fabrication, automotive, or construction, having a quality welding machine is vital. Understanding how these machines function can lead to more effective use and better results. This guide explores the types, features, and applications of welding machines.
Choosing the right welding machine is vital for project success. Consider factors such as the materials and thickness when making a decision. Weight and portability are also important. For instance, a lightweight MIG welder is excellent for on-site jobs, while a heavier TIG machine offers stability for intricate tasks.
Safety is crucial in welding operations. Understanding the hazards associated with welding machines can prevent accidents. Always wear protective gear, including gloves, masks, and protective clothing. This helps protect against burns, sparks, and harmful fumes. Additionally, ensure proper ventilation in the workspace.
Different Types of Welding Machines
Welding machines come in several types. Each type serves specific tasks. The most common categories include MIG, TIG, and Stick welding. MIG stands for Metal Inert Gas. This type uses a continuous wire feed. It works well for thin materials. Therefore, beginners often find it easier to learn.
On the other hand, TIG means Tungsten Inert Gas. This method provides more control over the welding process. Skilled welders often prefer it for intricate designs. It uses a non-consumable tungsten electrode. This element allows for precise and clean welds. Hence, it excels in intricate and detailed work.
Stick welding, or Shielded Metal Arc Welding (SMAW), is another option. This technique employs a consumable electrode coated in flux. This creates a shielding gas when it melts, protecting the weld area from contamination. Stick welding remains popular in construction and metalworking. It adapts well to outdoor conditions and various materials, making it versatile.
In addition to these three types, there are hybrid machines that combine functionalities. These units can switch between different modes. This versatility saves time and money. Moreover, it enables users to handle various projects without needing multiple machines. Thus, it is a worthy investment for serious professionals.
Key Features to Consider
When selecting a welding machine, several features require consideration. First, amperage range is crucial. A wider range allows for versatility in projects. A unit with adjustable amperage accommodates different metal thicknesses. Consequently, operators can achieve better weld quality.
Portability also plays a significant role in the decision-making process. Some projects require moving the machine. Therefore, lightweight models with sturdy carrying handles make a difference. Many manufacturers offer compact options for easy transport. This feature enhances flexibility on job sites.
Additionally, the duty cycle is an important specification. It indicates how long the machine can run before needing a cooldown period. Higher duty cycles facilitate long welding sessions. They are essential for larger projects that require extended use. Therefore, evaluating duty cycles becomes vital.
Another feature to consider is the ease of use. Many modern welding machines come equipped with user-friendly controls. Digital displays and preset settings simplify operation. This ease of use is especially helpful for beginners or those less experienced. Consequently, selecting an intuitive model can speed up the learning curve.
Furthermore, safety features must not be overlooked. Welding generates heat and sparks, which can pose risks. Machines with overload protection, thermal cutouts, and safety shut-off features enhance user safety. Investing in these additional safety measures reduces the risk of accidents, making the welding process more secure.
The Importance of Safety Measures
Safety in welding is paramount. The process involves high temperatures and sparks. Therefore, wearing proper protective gear is crucial. Items such as helmets, gloves, and fire-resistant clothing should always be worn. These pieces of equipment safeguard against burns and eye injuries.
Moreover, ensuring proper ventilation is essential. Welding generates harmful fumes and gases. Working in a well-ventilated space minimizes exposure to these hazards. Using fume extraction systems further enhances safety. They effectively capture harmful particles, protecting the welder’s health.
Training is another key aspect of safety. Operators should undergo proper training before using heavy equipment. This training includes recognizing hazards, understanding machine operation, and learning emergency procedures. Consequently, well-trained welders contribute to a safer work environment.
Additionally, regular equipment maintenance cannot be overlooked. A well-maintained welding machine operates more safely and efficiently. Regular checks for wear and tear help detect potential issues before they escalate. Properly maintaining machines enhances their lifespan and promotes safety.
Lastly, adhering to safety regulations is vital. Different industries have specific safety standards. Compliance ensures that welders operate within legal and safety parameters. This adherence not only protects the individual but also fosters a safer workplace for everyone involved.
Applications of Welding Machines
Welding machines are used across various sectors. Their applications span many fields, showcasing their versatility. The automotive industry heavily relies on welding for vehicle assembly. From car frames to exhaust systems, welding ensures strong and durable connections between components.
Additionally, construction projects make extensive use of welding machines. Steel structures, bridges, and buildings often require welding for assembly and reinforcement. These machines contribute to the structural integrity of essential infrastructures. Skilled welders take pride in ensuring stability and safety in construction.
Manufacturing also benefits from welding technology. Factories use welding machines to create everything from appliances to machinery parts. This process allows for high production efficiency. Therefore, welding machines enhance productivity and reduce lead times in manufacturing operations.
Art and sculpture present another area where welding shines. Artists use welding to create intricate metal sculptures. The ability to combine different materials allows for unique designs. Thus, welding expands the horizons of creativity in the art world.
Furthermore, shipbuilding relies on welding machines significantly. The construction of vessels involves joining large metal sheets and sections. Strong welds ensure the safety and durability of ships. Consequently, the maritime industry depends on skilled welders for quality construction.
Choosing the Right Welding Machine
Selecting the right welding machine can be overwhelming. Many factors need consideration to ensure proper selection. Initially, project requirements should guide the choice. The thickness and type of material will determine the welding process needed.
Next, budget plays a crucial role. Different machines come with varying price points. Investing in a higher-quality machine often pays off in the long run. Such machines tend to last longer and provide better performance.
Additionally, brand reputation should not be ignored. Well-established manufacturers often offer reliable options. Reading reviews and testimonials can provide valuable insights. Researching product specifications helps in making informed decisions.
Moreover, considering the skill level of the intended user is essential. Beginners may benefit from user-friendly machines with built-in features. More advanced users might want machines that offer sophisticated settings and controls.
Lastly, availability of customer support and warranty matters. A reputable manufacturer provides assistance when needed. This support proves invaluable in resolving technical issues. A solid warranty can offer peace of mind regarding the machine’s durability.
The Future of Welding Technology
The future of welding technology looks promising. Innovations are continually shaping the industry. Advancements in automation are particularly noteworthy. Robotic welding machines are becoming increasingly popular. They ensure precision and speed in various applications.
Moreover, advancements in materials are noteworthy. New welding consumables and techniques enhance the quality of welds. For example, resistant materials are being developed for high-stress applications. These innovations elevate the standards in welding.
Digital technology is also making waves. Machines equipped with smart features aid in monitoring and performance analysis. Real-time data allows welders to make informed adjustments on the spot. Consequently, this leads to higher quality welds and improved efficiency.
Sustainability is another driving factor in welding technology. Companies are exploring eco-friendly welding methods. These methods minimize waste and reduce emissions. This focus on sustainability will likely influence future developments.
Furthermore, the rise of additive manufacturing is reshaping the landscape. New welding techniques are being integrated into 3D printing processes. This evolution opens doors to unprecedented design possibilities. The convergence of these technologies could redefine traditional manufacturing methods.
Conclusion
In conclusion, welding machines are essential tools across multiple sectors. Their ability to join materials securely and efficiently is unmatched. Understanding the different types, features, and applications of these machines can lead to informed decisions. The safety measures that must be in place reinforce the importance of proper usage and training.
Choosing the right welding machine requires careful consideration. Evaluating project requirements, budget constraints, and skill levels is crucial. Embracing the advancements in welding technology will undoubtedly benefit industry professionals. As the world of welding continues to evolve, staying informed remains critical.
Ultimately, welding machines will remain pivotal in shaping industries and art forms alike. Investing in quality machines and adopting innovative practices will lead to success. Therefore, understanding welding machines is not just beneficial but essential for any aspiring welder or industry professional.