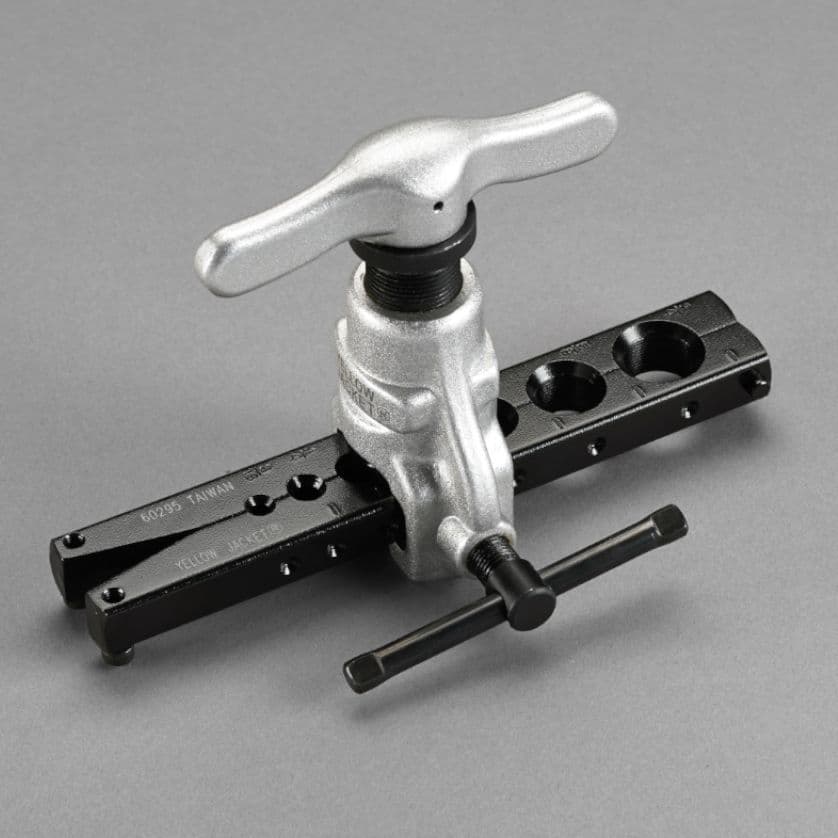
Flaring Tool: Essential Knowledge for Professional Results
Understanding the Basics of Flaring Tools
Working with copper and brass tubing requires specialized tools to create secure connections. A flaring tool stands as the most crucial implement for creating precise flared ends on metal tubing. Professional mechanics and plumbers rely on flaring tools to ensure leak-free connections in brake lines and plumbing systems. The basic flaring tool kit includes a yoke, flaring bars, and various sizing adapters for different tubing dimensions. Modern flaring tools come equipped with measurement markings that guarantee consistent flare depths across multiple connections.
The market offers both manual and hydraulic flaring tools to accommodate different working preferences and project scales. Quality flaring tools feature hardened steel construction to maintain precision through years of repeated use. Proper maintenance of flaring tools involves regular cleaning and lubrication of moving parts to prevent wear. Storage considerations play a vital role in preserving the accuracy of flaring tools over time. Different flaring standards exist worldwide, making versatile tools essential for international applications. Understanding local plumbing and automotive codes helps determine the appropriate flaring tool specifications for each job.
Types of Flares and Their Applications
Single flares create a basic outward bend that works well for low-pressure applications in residential settings. Double flares provide enhanced sealing capability through a two-step process that reinforces the connection point. Bubble flares, popular in European vehicles, offer superior sealing properties for brake line applications. Each flare type serves specific purposes based on pressure requirements and industry standards.
Professional technicians must match flare types to manufacturer specifications for warranty compliance. ISO flares meet international standards and ensure compatibility across different equipment brands. The automotive industry primarily uses SAE standard flares for consistency in repair work. Proper flare selection affects the longevity and safety of fluid transmission systems. Metal compatibility plays a crucial role in choosing appropriate flaring techniques. Temperature fluctuations influence the selection of flare types for specific applications.
Essential Steps for Perfect Flaring Technique
Clean cuts create the foundation for successful flaring operations in any application. Deburring removes sharp edges that could compromise the integrity of the final flare. Proper measurement ensures consistent flare depths across multiple connections in a system. The correct positioning of tubing in flaring bars prevents distortion during the flaring process. Steady pressure application helps achieve uniform flare formation without material stress points. Regular inspection between steps catches potential issues before they become permanent problems. Testing procedures verify the quality of completed flares before system integration. Professional results depend on following manufacturer-specified sequences for each flare type. Attention to detail during setup prevents common flaring mistakes and rework requirements. Time investment in proper technique pays dividends through reduced material waste.
Common Mistakes and Troubleshooting
Over-tightening leads to material distortion and potential failure points in completed flares. Improper alignment results in uneven flares that may leak under pressure conditions. Contamination from debris can compromise the sealing surface of finished flares. Incorrect tool selection often causes frustration and poor quality results. Material preparation errors account for many failed flaring attempts in practice. Temperature extremes during flaring can affect the final quality of connections. Rush jobs typically produce substandard results that require costly corrections later. Tool maintenance issues frequently contribute to inconsistent flaring outcomes. Understanding failure modes helps technicians prevent common flaring problems. Experience teaches valuable lessons about avoiding typical flaring pitfalls.
Professional Tools and Equipment Selection
Professional-grade flaring tools offer superior precision compared to budget alternatives. Hydraulic systems provide consistent pressure application for high-volume flaring operations. Digital measuring devices ensure accurate flare depths across multiple connections. Quality control equipment helps verify flare specifications before installation. Investment in proper tools pays dividends through improved efficiency and reliability. Modern flaring systems incorporate safety features that protect operators and materials. Tool manufacturers continue developing innovative solutions for challenging flaring applications. Material-specific tools help achieve optimal results with different types of tubing. Calibration requirements ensure continued accuracy in professional flaring operations. Regular tool upgrades keep pace with evolving industry standards.
Safety Considerations and Best Practices
Protective equipment safeguards operators during flaring operations in professional settings. Proper ventilation removes potentially harmful metal particles from the work area. Regular tool inspection prevents accidents caused by equipment failure. Organized workspaces contribute to safer flaring operations and better results. Emergency procedures should remain readily available in professional flaring operations. Training programs help maintain safety awareness among technical staff members. Material handling guidelines prevent injuries during flaring operations. Documentation requirements ensure compliance with safety regulations in commercial settings. Risk assessment procedures identify potential hazards before work begins. Standard operating procedures guide safe flaring practices.
Industry Standards and Regulations
Regulatory compliance affects flaring tool selection in commercial applications. International standards guide the development of modern flaring tools and techniques. Quality control requirements vary across different industries and applications. Documentation practices ensure traceability in professional flaring operations. Certification programs validate technical competency in flaring operations. Industry associations provide valuable resources for flaring standards updates. Compliance testing verifies adherence to regulatory requirements in commercial settings. Standard specifications guide material selection for different flaring applications. Technical committees continually update flaring standards to reflect new technologies. Professional certifications demonstrate commitment to industry best practices.
Advanced Techniques and Specialized Applications
High-pressure applications require specialized flaring techniques and tools. Custom flaring solutions address unique challenges in industrial settings. Aerospace applications demand precision flaring techniques for safety-critical systems. Marine environments present unique challenges for flaring operations and materials. Temperature extremes require specialized flaring techniques and material considerations. Corrosive environments necessitate careful material selection and protection measures. Complex geometries demand advanced flaring techniques and specialized tools. Quality assurance procedures verify compliance with stringent industry requirements. Innovation drives the development of new flaring techniques and applications. Specialized training programs prepare technicians for advanced flaring operations.
Industry Standards and Quality Control
Regulatory requirements guide flaring tool selection in commercial applications. International standards ensure consistency across different regions and industries. Quality control procedures verify compliance with industry specifications and requirements. Professional certification programs validate technical competency in flaring operations. Documentation practices ensure traceability in commercial flaring operations. Testing procedures confirm proper operation before system integration. Industry associations provide valuable resources for technical standards updates.
Compliance testing verifies adherence to regulatory requirements in commercial settings. Standard specifications guide material selection for different applications. Technical committees continuously update standards to reflect new technologies. Professional certifications demonstrate commitment to industry best practices. Regular audits ensure continued compliance with industry standards. Quality management systems track performance metrics across operations.
Advanced Applications and Specialized Tools
High-pressure systems require specialized flaring tools for optimal performance. Aerospace applications demand precision tools meeting strict industry standards. Marine environments need corrosion-resistant tools for long-term reliability. Custom solutions address unique challenges in industrial applications. Specialized training prepares technicians for advanced flaring operations. Quality assurance procedures verify compliance with stringent requirements. Innovation drives development of new flaring techniques and tools. Temperature extremes require specialized tools and techniques for success. Corrosive environments demand careful material selection and protection. Complex geometries need advanced tools for proper flare formation. Professional expertise guides selection of specialized equipment. Technical specifications ensure proper tool selection for applications. Industry demands shape development of specialized solutions.
Future Trends in Flaring Technology
Automation technologies streamline commercial flaring operations in modern facilities. Digital integration improves quality control in professional flaring applications. Smart tools provide real-time feedback during flaring operations. Environmental considerations drive innovations in flaring tool design. Material science advances create new opportunities for flaring applications. Industry demands shape the evolution of flaring technology and techniques. Artificial intelligence assists in quality control for commercial flaring operations. Sustainability concerns influence the development of new flaring methods. Remote monitoring capabilities enhance oversight of flaring operations. Market trends indicate continued growth in specialized flaring applications.
Conclusion: The Essential Role of Flaring Tools in Modern Plumbing
In conclusion, flaring tools stand as an indispensable asset in the toolkit of any plumbing professional or DIY enthusiast. Their ability to create strong, reliable connections between pipes makes them essential for ensuring the integrity of any plumbing system. The process of flaring not only enhances the functionality of pipelines, particularly for rigid copper and aluminum materials, but it also contributes significantly to the overall safety and efficiency of plumbing operations.
Utilizing a flaring tool properly requires not just an understanding of the instrument itself, but also a measure of skill and precision. The procedure ensures that joints are secure and leak-free, which is paramount in preventing water loss and potential property damage. Moreover, the ease of use that modern flaring tools offer—combined with their ability to produce consistent and accurate flares—empowers both novice and experienced plumbers to approach their tasks with confidence.
As plumbing technologies continue to evolve, so too does the purpose and design of flaring tools. Whether you’re dealing with HVAC systems, refrigeration lines, or traditional plumbing projects, investing in a high-quality flaring tool can make a significant difference in the long-term success of your installations. Moreover, as sustainable practices gain traction across various industries, the emphasis on efficiency and durability in plumbing installations becomes increasingly paramount—again highlighting the necessity of effective tools like flaring devices.
In summary, flaring tools not only simplify the process of connecting pipes but also play a critical role in upholding safety standards and promoting effective plumbing practices. As we move forward, the continued enhancement of these tools will undoubtedly contribute to advancements in plumbing methodologies, ensuring that both professionals and homeowners can maintain robust and reliable water systems for years to come.