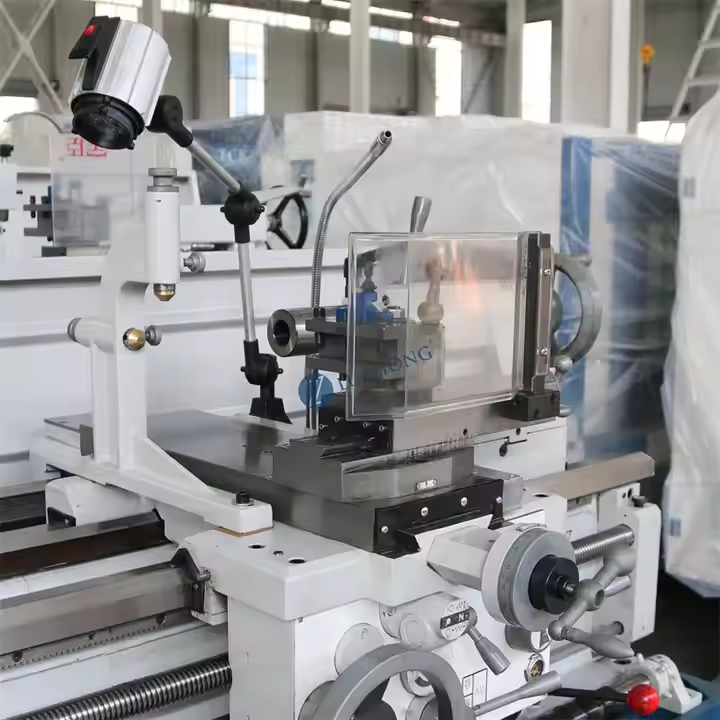
Mastering Lathe Machines: From Basics to Advanced Applications
Mastering Lathe Machines: From Basics to Advanced Applications
Manufacturing industries rely heavily on lathe machines for creating precise cylindrical parts and components. These versatile machines shape materials through rotary motion and cutting tools with remarkable accuracy. Modern lathes combine traditional craftsmanship with advanced technology to meet diverse manufacturing needs. Skilled operators can produce intricate parts ranging from simple bolts to complex aerospace components. The evolution of lathe technology continues to expand manufacturing capabilities worldwide.
Lathe machines stand as the cornerstone of modern manufacturing, shaping materials with precision and versatility. These powerful tools transform raw materials into precise components through controlled cutting and spinning operations. Manufacturing industries rely heavily on lathes to produce everything from simple bolts to complex mechanical parts.
Historical Development and Basic Operating Principles
Ancient civilizations first developed primitive lathes for woodworking applications thousands of years ago. The Industrial Revolution brought significant improvements to lathe design and operational capabilities. Steam power replaced manual operation, increasing productivity and precision in manufacturing processes. Metal lathes emerged as essential tools for producing standardized parts during industrialization. Modern electric motors now provide consistent power for smooth, controlled machining operations. Computer controls enhance precision and repeatability in contemporary lathe operations. The basic principle involves rotating workpieces against stationary cutting tools to remove material.
Work-holding devices secure materials while they spin at carefully controlled speeds. Different cutting tools create various shapes and features on rotating workpieces. Precision measurements ensure accurate dimensions throughout machining processes. Modern sensors monitor cutting conditions and adjust parameters automatically. Advanced lubricating systems protect moving parts and extend machine life significantly. Variable speed controls allow operators to optimize cutting conditions for different materials. Safety features protect operators while maintaining high productivity levels.
Essential Components and Their Functions in Modern Lathes
The headstock houses the main spindle and drive system for rotating workpieces. Chucks grip materials securely during high-speed rotation and cutting operations. The tailstock supports longer workpieces and holds drilling tools precisely. Carriage systems move cutting tools along the workpiece with controlled precision. Tool posts hold various cutting implements at optimal angles for efficient machining. The lathe bed provides rigid support for all operational components. Feed screws enable precise movement of tools during cutting operations. Cross-slides move cutting tools perpendicular to the rotating workpiece.
Guide ways ensure smooth, accurate tool movement during machining processes. Control panels provide access to speed, feed, and depth adjustments. Cooling systems prevent overheating during extended cutting operations. Emergency stops ensure quick shutdown capabilities for safety purposes. Digital displays show real-time position and speed information clearly. Automated lubrication systems maintain smooth operation of moving parts.
Advanced Features and Capabilities
Computer numerical control systems automate complex machining operations with precision. Multi-axis capabilities enable sophisticated part production with minimal setup time. Advanced tool holders accommodate various cutting implements for different operations. Automatic tool changers reduce downtime between different cutting operations. High-pressure coolant systems improve cutting efficiency and tool life.
Advanced measurement systems ensure consistent part quality during production. Variable speed drives optimize cutting conditions for different materials. Electronic handwheels provide precise manual control when needed. Programming interfaces simplify creation of complex machining routines. Network connectivity enables remote monitoring and program updates. Diagnostic systems identify potential problems before failures occur. Energy-efficient designs reduce operational costs while maintaining performance. Advanced safety features protect operators during all machining processes. Tool wear monitoring prevents quality issues in finished parts.
Material Considerations and Cutting Parameters
Different materials require specific cutting speeds for optimal results. Tool selection impacts surface finish quality and machining efficiency significantly. Proper feed rates ensure consistent material removal without damaging tools. Cutting depth affects both productivity and surface finish quality. Cooling requirements vary based on material properties and cutting conditions. Tool geometry influences chip formation and surface finish characteristics. Material hardness determines appropriate cutting speeds and tool selections.
Chip control features prevent hazardous conditions during machining operations. Surface finish requirements influence cutting parameter selections. Tool life varies significantly based on material properties. Heat generation requires careful monitoring during machining processes. Vibration control ensures consistent quality in finished parts. Material grain structure affects cutting performance significantly. Work hardening characteristics influence machining strategies.
Types of Lathe Operations and Applications
Turning operations reduce the diameter of workpieces to specified dimensions. Facing creates flat surfaces perpendicular to the workpiece’s rotational axis. Threading cuts precise internal or external threads for screws and bolts. Boring enlarges and finishes internal holes to exact specifications. Drilling operations create holes along the workpiece’s central axis. Knurling creates textured patterns on cylindrical surfaces for better grip. Tapering produces angled surfaces for various mechanical applications. Parting cuts workpieces to specific lengths with precision. Chamfering breaks sharp edges for safety and functionality. Form turning creates complex profiles for specialized components.
Safety Considerations and Best Practices
Proper training remains essential for all lathe operators before handling these powerful machines. Safety glasses and face shields protect against flying metal chips and debris. Loose clothing poses serious hazards and should never be worn near lathes. Regular maintenance prevents mechanical failures that could cause accidents. Emergency stop buttons must remain easily accessible at all times. Proper tool selection and setup prevent dangerous operating conditions. Clean work areas reduce accidents and improve operational efficiency. Regular equipment inspections identify potential safety hazards early. Proper material handling techniques prevent injuries during loading and unloading. Clear documentation of safety procedures guides operators in emergency situations.
Proper training ensures safe operation of lathe equipment. Safety glasses and face shields protect operators from flying chips. Emergency stops must remain easily accessible at all times. Regular maintenance prevents dangerous equipment failures during operation. Clean work areas reduce accident risks significantly. Proper clothing prevents entanglement hazards during machine operation. Tool condition monitoring prevents dangerous breakage situations. Standard operating procedures guide safe machine usage. Regular safety inspections identify potential hazards early. Documentation requirements ensure compliance with safety standards. Personal protective equipment remains essential for all operators. Safe material handling procedures prevent lifting injuries. Proper cleanup procedures maintain safe working environments. Regular safety meetings reinforce proper operating practices.
Maintenance Requirements and Procedures
Regular cleaning prevents buildup of chips and cutting fluids. Lubrication schedules keep moving parts operating smoothly. Alignment checks ensure continued accuracy in machining operations. Tool wear monitoring prevents quality issues in finished products. Temperature monitoring protects sensitive components from damage. Vibration analysis identifies potential mechanical problems early. Electronic diagnostics catch control issues before failure occurs. Preventive maintenance schedules reduce unexpected downtime significantly. Documentation tracks maintenance activities and equipment health. Spare parts inventory ensures quick repairs when needed. Regular calibration maintains machining accuracy over time. Belt tension checks prevent drive system problems. Coolant concentration monitoring optimizes cutting performance. Chuck maintenance ensures reliable workpiece holding.
Troubleshooting Common Issues
Systematic approaches identify root causes of machining problems quickly. Surface finish issues often indicate incorrect cutting parameters. Dimensional accuracy problems may result from worn guide ways. Vibration problems can stem from multiple mechanical sources. Tool wear patterns help diagnose cutting parameter issues. Chuck problems affect workpiece holding security significantly. Control system errors require systematic diagnostic approaches. Coolant system issues affect cutting performance and tool life. Power supply problems impact machine performance significantly. Mechanical alignment issues cause accuracy problems in finished parts. programming errors lead to unexpected machine behavior. Sensor failures affect automatic operation capabilities. Network connectivity issues impact remote monitoring functions. Environmental factors influence machine accuracy and performance.
Future Trends and Technological Advancements
Artificial intelligence enhances automated decision-making capabilities in modern lathes. Virtual reality training systems improve operator skill development safely. Internet of Things connectivity enables predictive maintenance capabilities. Sustainable manufacturing practices reduce environmental impacts significantly. Advanced materials require innovative cutting solutions and techniques. Hybrid manufacturing combines traditional turning with additive processes.
Smart tools provide real-time feedback during machining operations. Augmented reality assists with setup and maintenance procedures. Energy efficiency improvements reduce operational costs continuously. Automated quality control systems ensure consistent product quality. Remote programming capabilities increase operational flexibility significantly. Advanced simulation tools improve process planning efficiency. Integration with robotics expands automation possibilities. Cloud-based solutions enhance data management capabilities.
Maximizing Productivity and Quality
Efficient setup procedures reduce non-productive time significantly. Proper tool selection optimizes cutting performance for different materials. Regular quality checks ensure consistent part production. Process optimization improves throughput while maintaining quality standards. Advanced measurement techniques verify part specifications accurately. proper documentation ensures repeatability of successful processes. Team training improves overall operational efficiency. Quality management systems track and improve production processes. Cost analysis identifies opportunities for efficiency improvements. Production scheduling optimizes machine utilization effectively. Inventory management ensures continuous production capability. Customer feedback drives continuous improvement efforts. Performance metrics guide process optimization efforts. Lean manufacturing principles reduce waste in production processes.