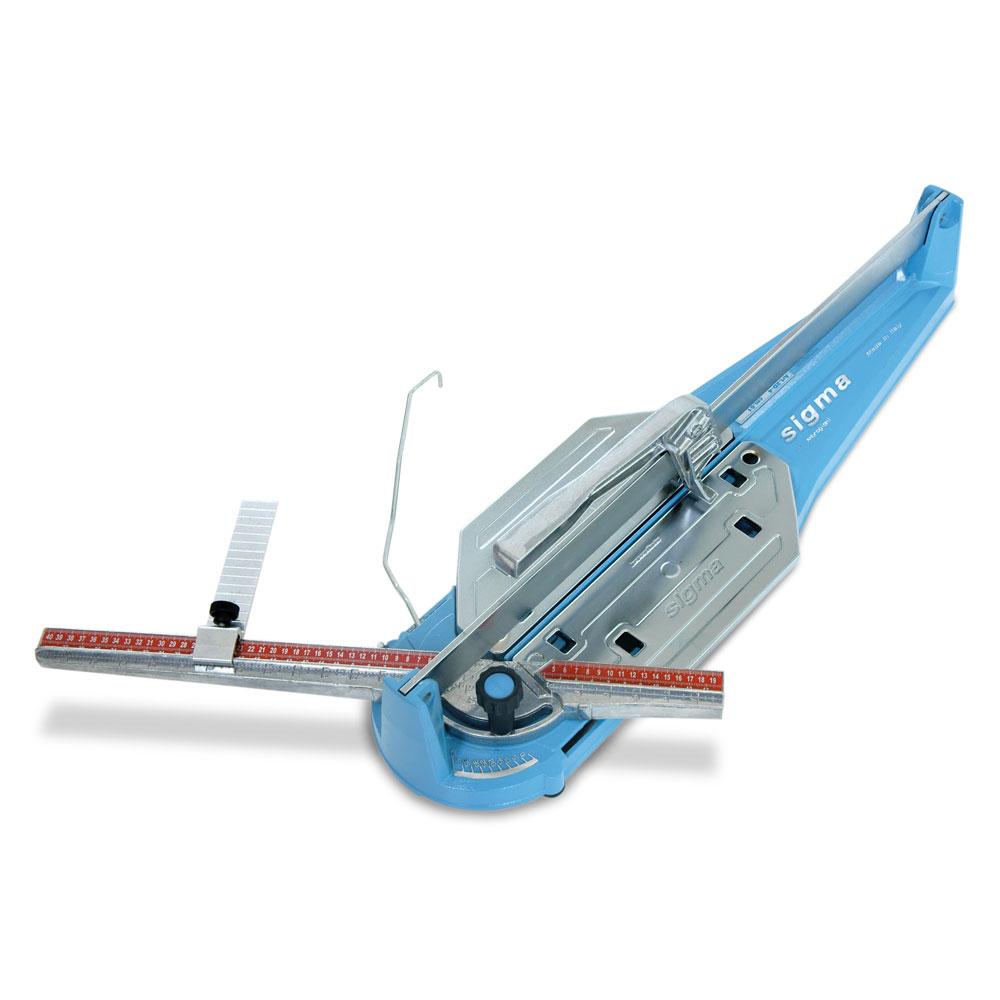
Tile Cutter: Essential Tools for Perfect Tile Installation
Evolution of Tile Cutting Tools
Tile cutting technology has evolved significantly from ancient manual methods to modern precision tools. Early civilizations used primitive hammers and chisels to shape tiles. The introduction of scoring wheels in the 19th century revolutionized tile cutter. Manual snap cutters emerged in the early 1900s, improving accuracy and efficiency. Additionally, wet saws appeared in the mid-20th century, enabling precise cuts through harder materials.
The development of diamond blades transformed cutting capabilities for modern materials. Furthermore, electric tile cutters brought power and precision to professional installations. Advancement in blade technology improved cut quality and reduced chipping. Modern tools feature laser guides and adjustable fences for enhanced accuracy. Moreover, portable cutting tools made job site work more efficient.
The introduction of water cooling systems reduced dust and extended blade life. Technological improvements continue to enhance cutting precision and safety. Therefore, modern tile cutters offer unprecedented accuracy and versatility. Digital measuring systems integrate with cutting tools for perfect alignment. Cordless options provide freedom of movement on job sites. These developments have made professional-quality tile cutting accessible to both contractors and DIY enthusiasts. The industry continues to innovate with new cutting technologies and materials. Consequently, tile cutting has become more precise and efficient than ever before.
Types of Tile Cutters Available
Various tile cutter tools serve different cutting needs and materials. Manual snap cutters work well for straight cuts in ceramic tiles. Electric wet saws handle porcelain and natural stone with precision. Additionally, handheld angle grinders make specialty cuts and adjustments. Rail cutters provide long, straight cuts for large format tiles. Furthermore, score-and-snap cutters offer portable cutting solutions. Professional-grade table saws feature adjustable cutting angles. Moreover, tile nippers create detailed cuts and curves. Jamb saws specialize in undercutting door frames. Similarly, hole saws create precise openings for pipes and fixtures.
Combination cutters offer multiple cutting options in one tool. Advanced models include water pumps for continuous cooling. Therefore, selecting the right cutter depends on project requirements. Specialized tools handle unique cutting challenges effectively. Portable cutters provide on-site cutting capabilities. Consequently, modern tile cutters meet diverse installation needs. Professional models offer enhanced features and durability. Entry-level tools suit occasional DIY projects well. The variety of available cutters ensures solutions for every application. These tools continue evolving to meet changing industry demands.
Essential Components of Tile Cutters
Quality tile cutters consist of several crucial components working together. The cutting wheel or blade serves as the primary cutting element. Sturdy base plates provide stable support during cutting operations. Additionally, guide rails ensure straight, accurate cuts. Water cooling systems prevent overheating in wet saws. Furthermore, measurement guides help achieve precise dimensions. Adjustable fences maintain consistent cutting angles. Similarly, miter gauges enable angled cuts with accuracy. Blade guards protect operators during cutting operations.
Moreover, water trays collect cooling water and debris. Anti-slip surfaces enhance safety during operation. Electric motors power professional cutting tools. Therefore, each component contributes to cutting accuracy. Laser guides improve cutting precision significantly. Bearing systems ensure smooth cutting motion. Consequently, quality components enhance cutting performance. Replacement parts extend tool service life. Regular maintenance keeps components functioning properly. Proper assembly ensures optimal cutting performance. These elements work together for precise results. The durability of components affects long-term reliability.
Proper Usage Techniques
Mastering proper cutting techniques ensures optimal results and safety. Correct measurement and marking precede any cutting operation. Proper tool selection matches cutters to specific materials. Additionally, blade inspection ensures safe cutting conditions. Setting up stable work surfaces prevents accidents. Furthermore, maintaining proper cutting speeds reduces material damage. Water levels require regular checking in wet saws. Similarly, blade alignment affects cut quality significantly. Practice improves cutting accuracy and efficiency.
Moreover, proper material support prevents breakage. Clean cutting surfaces enhance blade performance. Safety equipment protects operators during cutting. Therefore, following proper techniques improves results. Regular blade cleaning maintains cutting efficiency. Accurate measurements prevent material waste. Consequently, good technique produces professional results. Proper maintenance extends tool life significantly. Safety procedures prevent workplace accidents. These practices ensure consistent cutting quality. Proper storage protects equipment between uses. Regular inspection identifies potential problems early.
Safety Considerations
Safety remains paramount when operating tile cutting equipment. Protective eyewear shields against debris and water. Dust masks prevent inhalation of harmful particles. Additionally, hearing protection reduces noise exposure risk. Proper clothing prevents entanglement in moving parts. Furthermore, electrical safety prevents shock hazards. Proper ventilation removes dust and fumes. Similarly, clean work areas prevent accidents.
Regular equipment inspection ensures safe operation. Moreover, proper training reduces accident risks. Emergency procedures require clear understanding. Proper blade guards must remain in place. Therefore, safety awareness prevents workplace injuries. Proper tool maintenance ensures safe operation. First aid supplies should remain accessible. Consequently, safety measures protect operators effectively. Clear safety guidelines prevent accidents. Regular safety reviews maintain awareness. These practices protect both operators and equipment. Safety equipment requires regular inspection. Proper documentation records safety procedures.
Maintenance and Care
Regular maintenance keeps tile cutter performing optimally. Blade cleaning removes buildup and debris. Lubrication reduces wear on moving parts. Additionally, alignment checks ensure accurate cutting. Water systems require regular cleaning and inspection. Furthermore, motor maintenance prevents unexpected failures. Bearing systems need periodic lubrication. Similarly, guide rails require regular cleaning. Storage practices affect equipment longevity.
Moreover, rust prevention extends tool life significantly. Component replacement follows manufacturer schedules. Proper cleaning extends equipment life. Therefore, maintenance schedules prevent unexpected breakdowns. Regular inspection identifies wear patterns. Tool calibration maintains cutting accuracy. Consequently, proper maintenance reduces operating costs. Cleaning supplies remain readily available. Documentation tracks maintenance activities. These practices ensure reliable operation. Proper storage prevents equipment damage. Regular evaluation guides maintenance needs.
Choosing the Right Tile Cutter
Selecting appropriate tile cutter depends on project requirements. Material types influence cutter selection significantly. Project size determines required cutting capacity. Additionally, budget constraints affect equipment choices. Professional needs demand higher-quality tools. Furthermore, portability requirements influence selection. Cutting precision needs guide tool choices. Similarly, power requirements affect tool selection. Workspace limitations influence equipment size.
Moreover, frequency of use affects durability needs. Available accessories expand cutting capabilities. Brand reputation influences purchasing decisions. Therefore, careful selection ensures proper tool capability. Feature comparisons guide buying decisions. Price considerations balance against features. Consequently, proper selection improves project outcomes. Professional recommendations guide choices effectively. User reviews provide valuable insights. These factors determine optimal tool selection. Warranty coverage protects investments. Regular evaluation guides upgrade decisions.
Common Cutting Problems and Solutions
Various issues can affect tile cutter quality and efficiency. Chipping occurs from improper cutting techniques. Uneven cuts result from poor blade alignment. Additionally, blade wear affects cutting performance significantly. Material damage happens from excessive cutting speed. Furthermore, water flow problems affect wet saw performance. Improper measurements cause fitting problems. Similarly, blade wobble produces irregular cuts. Equipment vibration reduces cutting accuracy. Moreover, material waste increases from poor technique.
Temperature changes affect cutting performance. Dust control requires proper management. Therefore, understanding problems enables quick solutions. Regular maintenance prevents common issues. Proper technique reduces problem frequency. Consequently, quick solutions maintain productivity. Problem documentation guides future prevention. Regular evaluation identifies recurring issues. These practices improve cutting efficiency. Quality control maintains high standards. Solution documentation guides future repairs.
Advanced Cutting Techniques
Professional cutting skills develop through practice and experience. Complex patterns require advanced cutting methods. Curved cuts demand specialized techniques. Additionally, intricate designs need precise cutting control. Mosaic work requires detailed cutting ability. Furthermore, large format tiles need specific handling. Custom edges demand advanced cutting skills. Similarly, inlay work requires precision cutting. Specialty materials need adapted techniques.
Moreover, artistic designs require skilled cutting. Professional finish requires advanced knowledge. Therefore, skill development improves cutting capability. Practice enhances cutting precision significantly. Advanced tools enable complex cuts. Consequently, professional results require advanced skills. Specialized training improves capabilities. Experience guides technique development. These skills enhance project outcomes. Professional standards guide development. Regular practice maintains advanced skills.
Tile Cutting Innovations
Modern technology continues advancing tile cutting capabilities. Laser guidance systems improve cutting accuracy. Digital measuring tools enhance precision. Additionally, automated systems increase productivity significantly. New blade technologies improve cutting performance. Furthermore, dust control systems protect worker health. Battery technology enables cordless operation. Similarly, smart features enhance cutting precision. Advanced materials improve tool durability. Moreover, computer controls enable precise cuts.
Enhanced safety features protect operators. Industry innovations drive continuous improvement. Therefore, technology advances improve cutting capability. New features enhance user experience. Market demands drive innovation development. Consequently, cutting technology continues evolving. Research develops new cutting methods. Professional needs guide development direction. These advances improve installation quality. Future developments promise further improvements