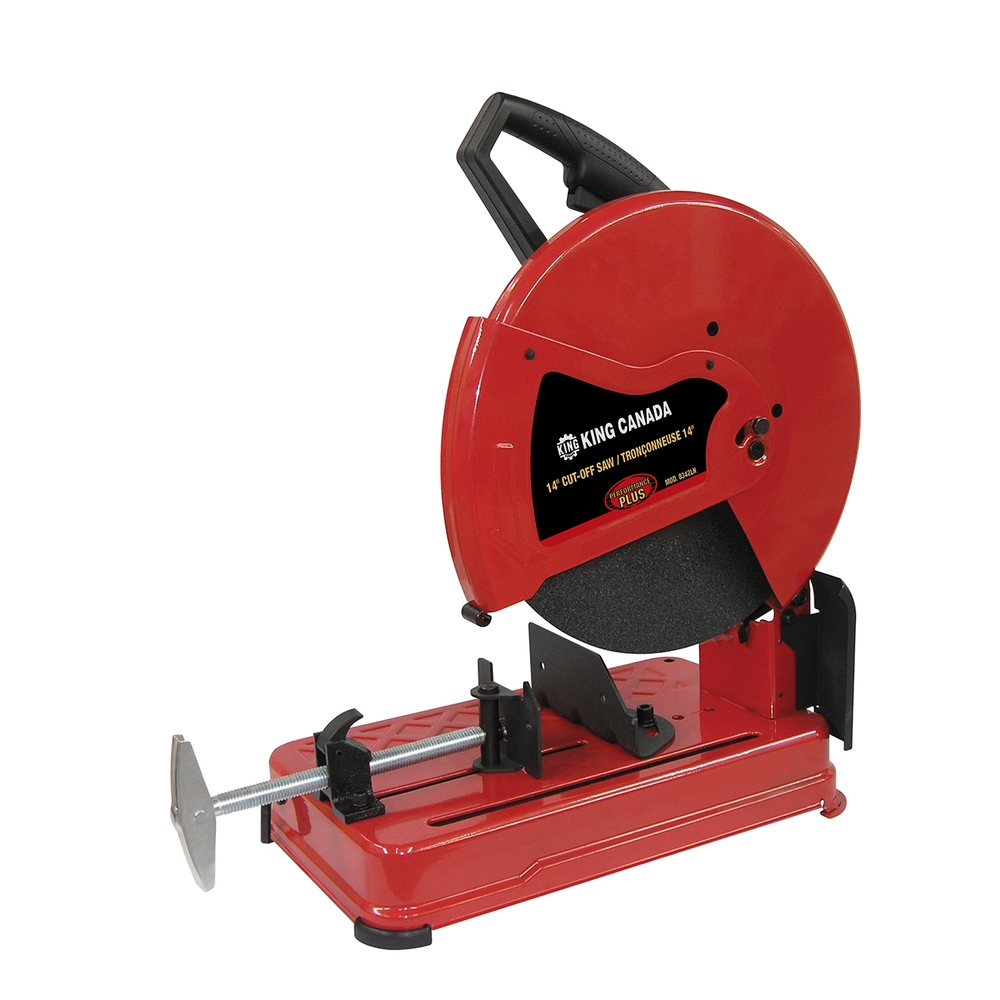
Cut-Off Saws: Precision Cutting for Professionals
Introduction: The Power and Versatility of Cut-Off Saws
Cut-off saws stand as indispensable tools in the world of metalworking, construction, and DIY projects. These powerful machines excel at making quick, precise cuts through a variety of materials, including metal, plastic, and masonry. Cut-off saws, also known as chop saws or abrasive saws, utilize a circular blade or abrasive disc to slice through materials with remarkable speed and accuracy. Their design allows for efficient, repetitive cuts, making them ideal for both industrial applications and home workshops. The versatility of cut-off saws extends beyond simple straight cuts, as many models offer the ability to make angled cuts, enhancing their utility in various projects.
As technology advances, modern cut-off saws incorporate features that improve safety, accuracy, and ease of use. These improvements have made cut-off saws more accessible to a wider range of users, from seasoned professionals to ambitious DIY enthusiasts. Understanding the capabilities and proper use of cut-off saws opens up new possibilities in metalworking and construction projects. Furthermore, the efficiency gained from using a cut-off saw can significantly reduce project completion times, allowing for increased productivity in both professional and personal endeavors. As we delve deeper into the world of cut-off saws, we’ll explore their types, components, applications, and best practices for use and maintenance.
Types of Cut-Off Saws: Choosing the Right Tool for the Job
Cut-off saws come in several varieties, each designed to excel in specific applications. The most common type is the abrasive cut-off saw, which uses a reinforced abrasive disc to cut through metals. These saws generate significant heat and sparks during operation, making them suitable for outdoor use or in well-ventilated areas. Next, cold saws employ a toothed blade that rotates at a slower speed, producing clean cuts with minimal heat and burrs. This makes cold saws ideal for precision work and situations where heat-affected zones must be minimized.
Dry cut saws represent a middle ground, using specialized carbide-tipped blades to cut metal without coolant, achieving cleaner cuts than abrasive saws with less heat generation. For masonry and concrete cutting, specialized cut-off saws with diamond-tipped blades offer unparalleled performance. These tools can handle the toughest materials with ease, making them essential for construction and renovation projects. Portable cut-off saws, often powered by batteries or gasoline engines, provide flexibility for job site use where electrical outlets may not be available. Each type of cut-off saw offers unique advantages, and selecting the right one depends on factors such as the materials being cut, the required precision, and the working environment. Understanding these differences allows users to choose the most appropriate tool for their specific needs, ensuring optimal performance and results in their cutting tasks.
Anatomy of a Cut-Off Saw: Understanding Key Components
Mastering the use of a cut-off saw begins with understanding its key components. At the heart of every cut-off saw lies a powerful motor, which drives the blade or disc at high speeds. The motor’s power output, typically measured in amps or horsepower, determines the saw’s cutting capacity and ability to handle tough materials. Connected to the motor, the arbor holds the cutting wheel securely in place, ensuring stable and accurate cuts. The blade guard, a critical safety feature, covers the majority of the blade, retracting only during cutting operations to minimize exposure to the spinning edge. Most cut-off saws feature a sturdy base or table that provides a stable platform for the material being cut.
Integrated into this base, a vice or clamp secures the workpiece firmly, preventing movement during cutting and enhancing both safety and accuracy. The handle or trigger mechanism allows users to control the saw’s operation, often incorporating safety features to prevent accidental activation. Many modern cut-off saws include adjustable fences or miter gauges, enabling angled cuts with precision. Dust collection ports help manage debris, connecting to vacuum systems for a cleaner work environment. Some advanced models feature laser guides or LED lights to improve cut line visibility. Understanding these components and their functions allows users to operate cut-off saws more effectively and safely, maximizing the tool’s potential in various cutting applications.
Selecting the Right Blade or Disc: Maximizing Cut-Off Saw Performance
The choice of blade or disc significantly impacts a cut-off saw’s performance and the quality of cuts it produces. For abrasive cut-off saws, reinforced resin-bonded discs come in various grits and compositions tailored to specific materials. Harder materials typically require coarser grits, while softer metals benefit from finer grits for smoother finishes. Cold saws utilize toothed blades, with the number of teeth and tooth geometry influencing cut quality and speed. More teeth generally result in smoother cuts but slower cutting speeds, while fewer teeth allow for faster cutting at the expense of some smoothness. Carbide-tipped blades, common in dry cut saws, offer a balance of cut quality and longevity, effectively cutting through various metals without coolant.
For masonry and concrete, diamond-tipped blades provide unmatched cutting performance, with different segment configurations optimized for various materials and cutting conditions. When selecting a blade or disc, consider factors such as the material being cut, desired cut quality, and frequency of use. Matching the blade’s diameter and arbor size to the saw is crucial for safe and effective operation. High-quality blades and discs, while often more expensive, can significantly improve cut quality and efficiency while lasting longer than cheaper alternatives. Regular inspection and timely replacement of worn blades or discs ensure consistent performance and safety. By carefully selecting and maintaining the appropriate cutting accessory, users can maximize their cut-off saw’s capabilities, achieving cleaner cuts and extended tool life.
Safety First: Essential Precautions for Cut-Off Saw Operation
Operating a cut-off saw safely requires adherence to essential precautions and best practices. Personal protective equipment (PPE) forms the first line of defense against potential hazards. Safety glasses or a face shield protect eyes from flying debris and sparks, while hearing protection guards against the high noise levels generated during cutting. Gloves offer protection from sharp edges and hot materials but should be used cautiously to avoid entanglement with the spinning blade. Proper clothing, including long sleeves and pants made from durable materials, provides additional protection. Before starting any cut, ensure the work area is clean and free from clutter, reducing the risk of trips and falls.
Secure the workpiece firmly in the saw’s vice or clamp to prevent movement during cutting. Never attempt to hold the material by hand while operating the saw. Maintain a stable stance and keep hands well away from the cutting area at all times. Allow the blade to reach full speed before initiating the cut, and avoid forcing the blade through the material. Instead, let the saw’s weight and momentum do the work. After completing a cut, wait for the blade to come to a complete stop before lifting it or removing cut pieces. Regularly inspect the saw for worn or damaged parts, replacing them promptly to maintain safe operation. Proper training and familiarization with the specific model of cut-off saw being used are crucial for safe operation. By consistently following these safety precautions, operators can minimize the risk of accidents and injuries while using cut-off saws effectively.
Mastering Cut-Off Saw Techniques: Achieving Precision and Efficiency
Developing proper techniques enhances both the precision and efficiency of cut-off saw operations. Start by marking cut lines clearly on the workpiece, using a permanent marker or scribe for visibility. When possible, position the material so that the cut-off saw’s blade enters the thinnest part of the profile first, reducing the cutting time and strain on the tool. For abrasive and dry cut saws, allow the weight of the saw head to do most of the work, applying only gentle pressure to guide the cut. Forcing the blade can lead to binding, overheating, and premature wear. When making multiple cuts of the same length, use a stop block or the saw’s built-in measurement features to ensure consistency without repeated measuring. For angled cuts, take extra care to secure the material properly and double-check angle settings before initiating the cut.
When cutting round stock, rotate the material slightly between cuts to prevent the blade from following the same path. Which can lead to uneven wear and potentially dangerous situations. For long or heavy materials, provide proper support on both sides of the cut to prevent binding or dropping of cut pieces. Practice smooth, controlled movements when operating the saw, avoiding jerky motions that can affect cut quality or cause the blade to bind. When cutting thin materials, consider stacking multiple pieces to increase efficiency, ensuring they are securely clamped together. By mastering these techniques and adapting them to specific materials and cutting requirements, operators can achieve better results while extending the life of their cut-off saw and blades.
Applications and Versatility: Exploring Cut-Off Saw Uses
Cut-off saws demonstrate remarkable versatility across a wide range of applications in various industries and DIY projects. In metalworking shops, these tools efficiently cut steel bars, pipes, and profiles to length, preparing materials for welding or further fabrication. Construction sites rely on cut-off saws for trimming rebar, cutting metal studs, and sizing pipe for plumbing installations. The automotive industry utilizes cut-off saws in both manufacturing and repair processes, cutting exhaust pipes, frame components, and custom parts. In the realm of DIY and home improvement, cut-off saws prove invaluable for tasks such as cutting metal fencing, trimming bolts to length, and fabricating custom brackets or hardware.
Sculptors and metal artists employ these versatile tools to shape raw materials into intricate forms, leveraging their precision cutting capabilities. The ability to make angled cuts expands their utility in creating custom joints and fittings for various projects. Masonry cut-off saws excel in landscaping and hardscaping applications, precisely cutting pavers, bricks, and concrete blocks for pathways and retaining walls. Restoration and renovation projects benefit from cut-off saws when removing old fasteners, cutting damaged structural elements, or modifying existing metalwork. The portability of some models allows for on-site cutting in locations where bringing materials back to a shop would be impractical. From precision industrial applications to creative DIY endeavors. Cut-off saws continue to prove their worth as essential tools in the modern workshop and construction site.
Maintenance and Care: Ensuring Longevity of Your Cut-Off Saw
Proper maintenance ensures the longevity and reliable performance of cut-off saws. Begin with regular cleaning after each use, removing metal shavings, dust, and debris from all parts of the saw. Pay special attention to the motor vents, keeping them clear to prevent overheating. For abrasive saws, periodically check the wheel flanges and arbor for wear. Replacing them if necessary to maintain proper wheel alignment. Lubricate moving parts according to the manufacturer’s recommendations, typically focusing on pivot points and sliding components. Regularly inspect the power cord for any signs of wear or damage. Replacing it if any issues are found to prevent electrical hazards. Check and tighten all bolts and adjustments periodically to ensure the saw remains properly aligned and calibrated.
For saws with a coolant system, clean and refill the coolant reservoir as needed, using the appropriate type and mixture of coolant. Inspect the blade guard mechanism regularly, ensuring it moves freely and provides proper coverage during operation. Replace worn or damaged blades promptly to maintain cutting efficiency and safety. Store the cut-off saw in a dry environment to prevent rust and corrosion, especially on critical components like the table and fence. Consider having the saw professionally serviced annually, particularly for models used in high-volume or demanding applications. By adhering to these maintenance practices. Users can significantly extend the life of their cut-off saw, ensuring it remains a reliable and effective tool for years to come.
Troubleshooting Common Issues: Overcoming Cut-Off Saw Challenges
Even well-maintained cut-off saws may encounter issues that require troubleshooting. One common problem is blade wobble, which can result from a bent arbor, worn bearings, or an improperly mounted blade. Addressing this issue may involve replacing damaged components or simply ensuring the blade is correctly seated and tightened. Excessive vibration during operation often indicates an unbalanced or damaged blade, requiring replacement to restore smooth cutting action. If the saw fails to start, check the power source, cord, and switch for any faults. Tripped circuit breakers or worn brushes in the motor can also prevent startup. Burning or scoring of the cut surface may indicate a dull blade or incorrect cutting speed for the material. Adjusting the speed or replacing the blade with a more appropriate type can resolve this issue.
Binding during cuts often results from misalignment of the fence or vise, or from the material shifting during cutting. Ensuring proper alignment and secure clamping can prevent this problem. For saws with a coolant system, poor coolant flow may lead to overheating and reduced cut quality. Cleaning the coolant lines and nozzles or replacing the coolant pump can restore proper function. If the saw lacks power or stalls during cuts, the cause may be a worn drive belt, motor issues, or attempting to cut material beyond the saw’s capacity. Regular maintenance and operating within the tool’s specified limits help prevent many of these issues. By understanding and addressing these common problems, users can maintain their cut-off saw’s performance and extend its useful life.
Innovations and Future Trends: The Evolving World of Cut-Off Saws
The cut-off saw industry continues to evolve, driven by technological advancements and changing user needs. Recent innovations focus on improving safety, precision, and ease of use. Laser guide systems, once a premium feature, are becoming standard on many models, enhancing cut accuracy. Advanced blade materials and designs offer longer life and improved cutting performance across a wider range of materials. Some manufacturers are integrating smart technology into their saws, with features like automatic speed adjustment based on material density and thickness. This technology optimizes cutting performance while extending blade life. Cordless cut-off saws powered by high-capacity lithium-ion batteries are gaining popularity, offering increased portability without sacrificing power. Improved dust collection systems address health and safety concerns, with some models featuring built-in vacuum attachments for cleaner operation.