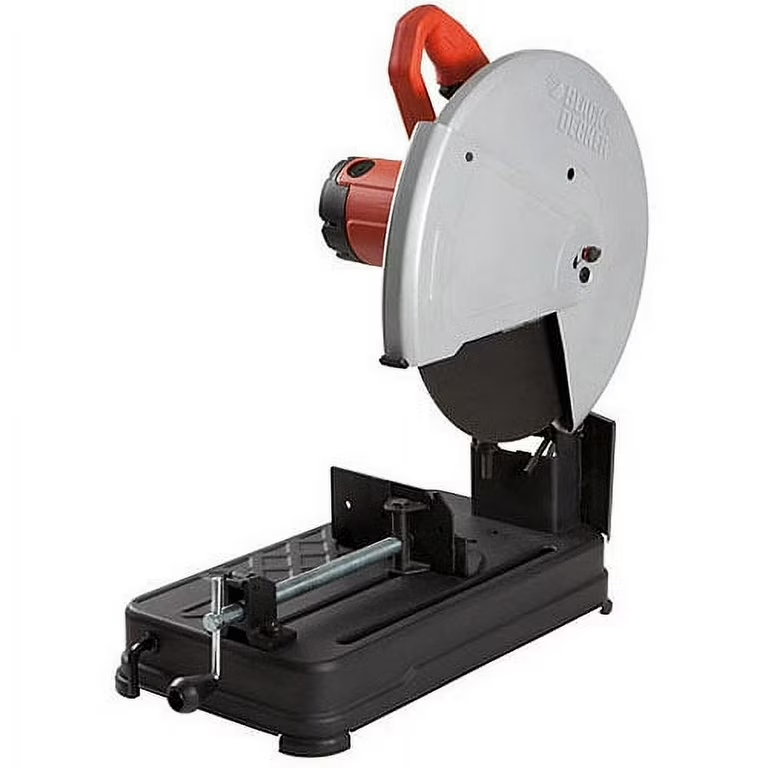
A Comprehensive Guide to Chop Saw
Understanding the Chop Saw: A Powerful Tool for Precise Cuts
Chop saws stand as indispensable tools in the world of woodworking and metalworking, offering unparalleled precision and efficiency for crosscutting materials. These powerful machines feature a circular blade mounted on a hinged arm that pivots downward to make clean, straight cuts. Chop saws come in two main varieties: wood-cutting models with toothed blades and metal-cutting versions with abrasive discs. The key advantage of a chop saw lies in its ability to make quick, accurate cuts at precise angles, making it ideal for tasks such as trimming lumber, cutting molding, or slicing through metal pipes and bars.
Unlike traditional handsaws or circular saws, chop saws provide a stable base and guided cutting motion, ensuring consistency across multiple cuts. Additionally, many models feature adjustable fences and miter gauges, allowing users to set specific angles for more complex cutting tasks. The power and precision of chop saws make them essential in construction sites, workshops, and manufacturing facilities where speed and accuracy are paramount. As technology advances, modern chop saws incorporate features like laser guides, dust collection systems, and ergonomic designs, further enhancing their utility and user-friendliness.
Types of Chop Saws: Choosing the Right Tool for the Job
Chop saws come in various types, each designed to excel in specific cutting applications. The most common variety is the compound miter saw, which allows for both vertical chopping motions and angled miter cuts. This versatility makes compound miter saws popular among carpenters and DIY enthusiasts for tasks like cutting crown molding or picture frames. Sliding compound miter saws take this concept further by incorporating a sliding arm, enabling the saw to handle wider workpieces. For metalworking, abrasive chop saws use specialized blades to cut through steel, aluminum, and other metals with ease.
These saws often feature spark deflectors and clamps to ensure safe and precise cutting of metal stock. Tile saws, a specialized type of chop saw, use diamond-tipped blades to cut through ceramic and stone tiles cleanly. Some manufacturers offer multi-material chop saws that can switch between wood and metal cutting modes, providing versatility for users who work with various materials. When selecting a chop saw, consider factors such as blade size, motor power, and cutting capacity to ensure the tool meets specific project requirements. Additionally, features like bevel capabilities, depth stops, and laser guides can greatly enhance the functionality and precision of the saw.
Essential Features of a Quality Chop Saw
A high-quality chop saw boasts several key features that contribute to its performance and user experience. First and foremost, a powerful motor forms the heart of any good chop saw, providing the necessary torque to cut through tough materials effortlessly. Blade quality plays a crucial role in the saw’s cutting ability, with carbide-tipped blades offering superior durability and sharpness for wood cutting, while abrasive discs excel in metal applications. A sturdy base and fence system ensure stability during cuts, reducing vibration and improving accuracy. Many premium chop saws include adjustable depth stops, allowing users to make repetitive cuts or dados with precision.
Bevel and miter adjustment mechanisms should operate smoothly and lock securely to maintain accurate angles throughout the cutting process. Dust collection ports help maintain a clean work area and improve visibility during cuts. Safety features such as blade guards, electric brakes, and lock-off switches are essential for protecting the user during operation. Ergonomic considerations, including comfortable handles and easily accessible controls, contribute to reduced fatigue during extended use. Some advanced models incorporate digital displays for precise angle readings and laser guides for enhanced cut line visibility. When evaluating chop saws, these features collectively determine the tool’s overall quality and suitability for specific cutting tasks.
Safety Considerations When Operating a Chop Saw
Operating a chop saw requires strict adherence to safety protocols to prevent accidents and injuries. Proper personal protective equipment (PPE) forms the first line of defense, including safety glasses, hearing protection, and dust masks. Users should avoid loose clothing or jewelry that could become entangled in the saw’s moving parts. Before making any cuts, inspect the saw for damaged components, ensuring the blade guard functions correctly and the blade itself is sharp and free from defects. Secure the workpiece firmly against the fence and table using clamps when necessary, especially for smaller or irregularly shaped materials.
Maintain a safe distance from the blade, keeping hands and fingers well away from the cutting area. Allow the blade to reach full speed before initiating the cut, and avoid forcing the saw through the material, which can cause kickback or blade binding. After completing a cut, wait for the blade to come to a complete stop before raising the saw arm or removing the workpiece. Regular maintenance, including blade changes and adjustment checks, helps ensure the saw operates safely and efficiently. Proper workspace organization, with adequate lighting and a clean, clutter-free area around the saw, further contributes to a safe working environment. By following these safety guidelines, operators can minimize risks and focus on achieving precise, high-quality cuts with their chop saw.
Techniques for Achieving Precise Cuts with a Chop Saw
Mastering precise cutting techniques elevates the quality of work produced with a chop saw. Begin by properly aligning the workpiece against the fence and marking the cut line clearly. For improved accuracy, many professionals recommend cutting slightly outside the line and then sanding or planing to the exact dimension. When making miter cuts, use a scrap piece to test the angle setting before cutting the final workpiece. This practice ensures the miter gauge is calibrated correctly and helps avoid costly mistakes. For bevel cuts, take extra care to secure the workpiece, as the angled blade can cause it to shift during cutting.
Utilize stop blocks for repetitive cuts, ensuring consistency across multiple pieces. When cutting crown molding or other complex profiles, use a scrap piece to verify the compound angle settings before attempting the final cut. For cleaner cuts in wood, use a sharp blade with a high tooth count, and consider applying masking tape along the cut line to reduce splintering. When cutting metal, allow the abrasive blade to do the work without applying excessive pressure, which can cause overheating and reduce cut quality. Practice proper blade entry and exit techniques, lowering the blade slowly into the material and maintaining a steady pace throughout the cut. By refining these techniques and paying attention to details, users can achieve professional-grade results with their chop saw projects.
Maintaining and Caring for Your Chop Saw
Regular maintenance ensures optimal performance and longevity of a chop saw. Start by keeping the saw clean, removing dust and debris after each use with a brush or compressed air. Pay special attention to the motor vents, as clogged vents can lead to overheating and reduced efficiency. Lubricate moving parts according to the manufacturer’s recommendations, typically focusing on pivot points and slide mechanisms. Regularly check and tighten all bolts and screws, as vibration during operation can cause them to loosen over time. Inspect the power cord for any signs of wear or damage, replacing it if necessary to maintain safety. For the blade, clean it periodically with a specialized blade cleaner to remove pitch and resin buildup, which can affect cutting performance.
When changing blades, take the opportunity to clean the blade housing and check the arbor for any signs of wear. Maintain the accuracy of your saw by periodically checking and adjusting the miter and bevel settings using a quality square or angle gauge. If the saw features a laser guide, clean the lens and check its alignment regularly. For saws with a belt drive, inspect the belt tension and condition, replacing it if signs of wear are present. Proper storage in a dry environment, covered when not in use, protects the saw from dust and moisture. By implementing a regular maintenance routine, users can ensure their chop saw remains a reliable and precise cutting tool for years to come.
Advanced Applications: Beyond Basic Cutting
While chop saws excel at straightforward crosscuts, they also offer potential for more advanced applications. One such technique is cutting dadoes and rabbets by making multiple passes with the blade set to a specific depth. This method requires careful setup and often benefits from the use of a stop block to ensure consistent depth across all cuts. Some woodworkers use their chop saws for creating splined miter joints, enhancing the strength and appearance of corner joints in frames or boxes. By setting up a simple jig, a chop saw can be used to cut accurate tenons for joinery work.
In metalworking, specialized chop saws can perform tasks like cutting pipe at precise angles for plumbing or structural applications. Advanced users might employ their chop saws for cutting custom moldings by making multiple angled cuts to achieve complex profiles. When working with large panels, a chop saw can be used in conjunction with a circular saw to break down sheets efficiently, with the chop saw providing clean, square ends. Some craftsmen even use their chop saws for decorative purposes, creating intricate patterns through repeated angled cuts. By exploring these advanced applications, users can expand the versatility of their chop saw and tackle a wider range of projects with a single tool.
Comparing Chop Saws to Other Cutting Tools
Chop saws offer unique advantages when compared to other cutting tools, each with its own strengths and limitations. Unlike table saws, which excel at ripping long boards, chop saws specialize in crosscuts and angled cuts, providing greater precision and safety for these tasks. Circular saws offer portability but lack the stability and accuracy of a chop saw for repetitive or angled cuts. Band saws can handle curved cuts that chop saws cannot, but they struggle with the quick, clean crosscuts at which chop saws excel.
Reciprocating saws, while versatile for demolition work, cannot match the precision of a chop saw for finish carpentry. Jigsaws offer maneuverability for intricate cuts but lack the power and accuracy of a chop saw for straight cuts in thicker materials. For metalworking, chop saws with abrasive blades outperform hacksaws in terms of speed and consistency, especially when dealing with larger stock. However, angle grinders might be preferred for cutting metal in tight spaces or on-site where portability is crucial. Understanding these comparisons helps users select the most appropriate tool for specific cutting tasks, recognizing that while chop saws excel in many applications, they may not be the ideal choice for every cutting job.
Innovations and Future Trends in Chop Saw Technology
The world of chop saws continues to evolve, with manufacturers introducing innovations to enhance performance, safety, and user experience. One significant trend is the development of cordless chop saws, powered by high-capacity lithium-ion batteries, offering the convenience of portability without sacrificing power. Advanced dust collection systems are becoming more sophisticated, with some models featuring automatic activation and fine particle filtration to improve workplace air quality. Laser guide technology is evolving to provide more accurate and visible cut lines, with some saws incorporating dual lasers for enhanced precision. Digital angle readouts and electronic miter detents are improving the accuracy of angle cuts, reducing setup time and human error.
Some manufacturers are exploring the integration of smart technology, allowing saws to connect to mobile devices for maintenance tracking, usage statistics, and even remote operation in industrial settings. Materials science advancements are leading to lighter yet more durable saw components, improving portability without compromising stability. Blade technology continues to progress, with new tooth designs and materials offering cleaner cuts and longer life across various materials. As sustainability becomes a greater focus, expect to see more energy-efficient motors and eco-friendly manufacturing processes in future chop saw models. These innovations and trends point towards a future where chop saws become even more precise, versatile, and user-friendly tools in the world of cutting technology.
Selecting the Right Chop Saw for Your Needs
Choosing the ideal chop saw requires careful consideration of several factors to ensure it meets specific project requirements and user preferences. Begin by determining the primary materials to be cut, as this will influence the choice between wood-cutting and metal-cutting models. Next, consider the size of the workpieces typically handled, which will dictate the saw’s cutting capacity and whether a sliding compound miter saw might be necessary for wider boards. Evaluate the power requirements, ensuring the saw’s motor can handle the intended workload without straining. For those working in various locations, the weight and portability of the saw become important factors.
Consider the accuracy needs of the projects, possibly opting for models with advanced features like digital readouts or laser guides for precision work. Assess the available workspace, as larger saws with extended sliding capabilities require more room to operate effectively. Don’t overlook ergonomic features, especially for users who will operate the saw for extended periods. Budget considerations will also play a role, balancing the need for specific features against cost constraints. Finally, research brand reliability and after-sales support, as these factors can significantly impact long-term satisfaction with the tool. By carefully weighing these aspects, users can select a chop saw that not only meets their current needs but also accommodates future project requirements.