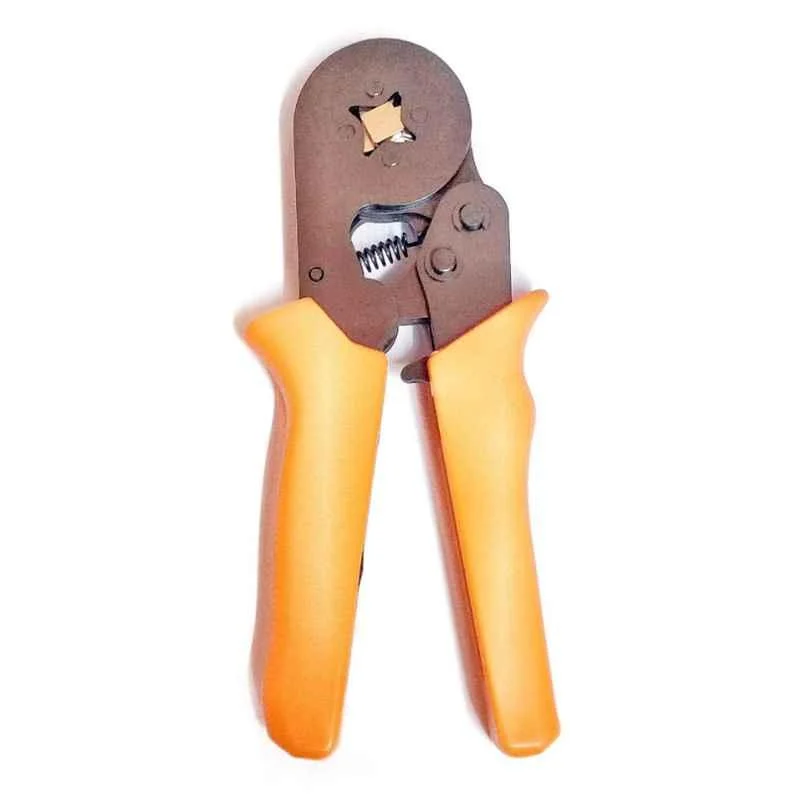
A Comprehensive Guide to Hand Crimping Tool
Understanding the Importance of Hand Crimping Tools in Electrical Work
Hand crimping tools play a crucial role in the world of electrical and electronic connections. These versatile instruments enable technicians, electricians, and DIY enthusiasts to create secure, reliable connections between wires and terminals without the need for soldering. The importance of proper crimping cannot be overstated, as it directly impacts the integrity and longevity of electrical systems. A well-executed crimp provides a gas-tight connection that resists corrosion and maintains consistent electrical conductivity over time.
Hand crimping tool come in various shapes and sizes, each designed for specific types of connectors and wire gauges. From automotive wiring harnesses to delicate electronic components, these tools find applications across a wide range of industries and projects. Understanding the principles behind crimping and the proper use of hand crimping tools is essential for anyone working with electrical connections, ensuring safety, reliability, and efficiency in their work.
Types of Hand Crimping Tools: Choosing the Right Tool for the Job
The market offers a diverse array of hand crimping tools, each tailored to specific connector types and applications. Ratchet crimpers, known for their precision and consistent crimping force, are popular for professional-grade work. These tools feature a ratcheting mechanism that ensures the crimp is fully completed before releasing, preventing under-crimping.
Plier-style crimpers, resembling traditional pliers, offer simplicity and versatility for lighter-duty applications. For more specialized needs, dedicated crimpers exist for coaxial connectors, insulated terminals, and non-insulated terminals. Modular crimpers, designed for telephone and data cables, feature interchangeable dies to accommodate various connector types.
Heavy-duty hydraulic crimpers, while not strictly hand tools, provide the force necessary for large-gauge wires and industrial-grade connectors. When selecting a hand crimping tool, consider factors such as the types of connectors used, wire gauges, frequency of use, and required precision. Professional electricians often maintain a collection of crimping tools to handle a wide range of connectors and wire sizes encountered in their work.
Anatomy of a Hand Crimping Tool: Key Components and Features
To effectively use and maintain a hand crimping tool, it’s essential to understand its key components. The jaws or dies form the business end of the tool, shaping the connector around the wire to create a secure connection. Many crimping tools feature interchangeable dies to accommodate different connector types and sizes. The handles provide leverage for applying the necessary force to complete the crimp. In ratchet-style crimpers, the ratchet mechanism ensures consistent pressure and prevents the tool from releasing until the crimp is fully formed.
Some advanced models incorporate a pressure adjustment feature, allowing users to fine-tune the crimping force for different materials and connector types. The pivot point, typically a bolt or pin, connects the two halves of the tool and serves as the fulcrum for the crimping action. Quality crimping tools often include comfort grips on the handles to reduce hand fatigue during extended use. Understanding these components helps users select the appropriate tool for their needs and properly maintain it for optimal performance and longevity.
Proper Crimping Technique: Ensuring Reliable Electrical Connections
Mastering the proper crimping technique is crucial for creating secure and reliable electrical connections. The process begins with selecting the appropriate connector and wire size for the application. Strip the wire carefully, removing just enough insulation to fit into the connector without exposing excess bare wire. Insert the stripped wire into the connector, ensuring it fully seats in the barrel.
Position the connector in the crimping tool, aligning it with the correct die size for a precise fit. Apply steady pressure to the handles, closing the tool completely to form the crimp. For ratchet-style crimpers, continue squeezing until the tool releases, indicating a complete crimp. Inspect the crimped connection visually, looking for a uniform compression around the barrel and ensuring no exposed wire strands. Gently tug on the wire to verify the connection’s strength.
For insulated connectors, check that the insulation has been properly compressed without cutting into the wire. Proper crimping technique also involves maintaining the tool, keeping the dies clean and free from debris that could affect crimp quality. By following these steps and practicing good technique, technicians can create consistently reliable connections across a wide range of electrical applications.
Common Mistakes and Troubleshooting in Hand Crimping
Even experienced technicians can encounter issues when crimping connections. Common mistakes include using the wrong size die for the connector, resulting in over- or under-crimping. Over-crimping can weaken the wire strands or damage the connector, while under-crimping fails to create a secure connection. Improper wire stripping is another frequent issue, either leaving too much insulation and preventing full insertion into the connector, or removing too much and risking short circuits.
Misalignment of the connector in the crimping tool can lead to asymmetrical crimps that may fail over time. To troubleshoot crimping problems, start by double-checking the compatibility of the wire, connector, and crimping tool. Inspect crimped connections closely, looking for signs of deformation, exposed wire strands, or inconsistent compression.
If issues persist, consider calibrating the crimping tool or replacing worn dies. For critical applications, perform pull tests to verify the strength of crimped connections. Maintaining a clean work environment and regularly inspecting tools for wear or damage can prevent many common crimping issues. When in doubt, it’s always better to cut off a questionable crimp and start over rather than risking a faulty connection in an electrical system.
Maintenance and Care of Hand Crimping Tools
Proper maintenance of hand crimping tools is essential for ensuring consistent performance and longevity. Regular cleaning is the first step in tool care, removing dirt, metal shavings. Other debris that can accumulate in the dies and moving parts. Use a soft brush or compressed air to clean hard-to-reach areas. For tools with moving parts, periodic lubrication with a light machine oil helps maintain smooth operation and prevent rust. Store crimping tools in a dry environment to prevent corrosion, ideally in a toolbox or case that protects them from impacts and dust.
Inspect the dies regularly for signs of wear or damage, as worn dies can lead to inconsistent crimps. Many quality crimping tools offer replaceable dies, extending the tool’s useful life. For ratchet-style crimpers, check the ratchet mechanism periodically to ensure it engages and releases properly. If the tool becomes difficult to use or produces inconsistent results, it may require professional servicing or calibration. By implementing a regular maintenance routine, technicians can ensure their hand crimping tools remain accurate and reliable for years of service.
Innovations and Future Trends in Hand Crimping Technology
The field of hand crimping tools continues to evolve, with manufacturers introducing innovations to improve efficiency, precision, and user experience. One significant trend is the integration of ergonomic design principles, resulting in tools that reduce hand fatigue and increase comfort during extended use. Some advanced crimpers now incorporate electronic pressure sensors and displays, allowing users to monitor and adjust crimping force precisely.
Battery-powered hydraulic crimpers are gaining popularity for their ability to deliver consistent, high-force crimps with minimal user effort. In the realm of quality control, manufacturers are developing crimping tools with built-in validation features. Such as crimp depth indicators or force measurement systems, to ensure each connection meets specified standards. The rise of modular crimping systems, allowing quick changes between different connector types and sizes, addresses the need for versatility in diverse work environments.
As the Internet of Things (IoT) expands into industrial tools, smart crimpers that can log data. Track maintenance needs, and even integrate with broader quality management systems are on the horizon. These advancements in hand crimping technology promise to enhance productivity. Improve connection reliability, and provide better documentation for critical electrical work.
Conclusion
Hand crimping tools stand as essential instruments in the toolkit of anyone working with electrical connections, from professional electricians to hobbyist makers. Their ability to create secure, long-lasting connections without the need for soldering makes them indispensable across a wide range of applications, from automotive wiring to telecommunications infrastructure. The diverse array of crimping tools available today reflects the complexity and specialization of modern electrical systems. With each type designed to meet specific connector and wire requirements.
Mastering the proper use of these tools involves not only understanding their mechanical operation but also developing the skill to execute precise, consistent crimps across various connector types and sizes. The importance of proper crimping technique cannot be overstated, as the integrity of electrical systems often hinges on the quality of individual connections. By following best practices in tool selection, crimping technique, and ongoing maintenance, technicians can ensure reliable performance and safety in their electrical work.
As technology continues to advance, hand crimping tools are evolving to meet new challenges. Incorporating features that enhance precision, efficiency, and quality control. From ergonomic designs that reduce user fatigue to smart tools . That integrate with digital systems, the future of hand crimping promises even greater capabilities and reliability. For professionals and enthusiasts alike, investing time in understanding and mastering hand crimping tools pays dividends in the form of high-quality electrical work that stands the test of time. As electrical systems become increasingly complex and ubiquitous in our daily lives. The humble hand crimping tool remains a fundamental link in the chain of reliable, efficient electrical connections.