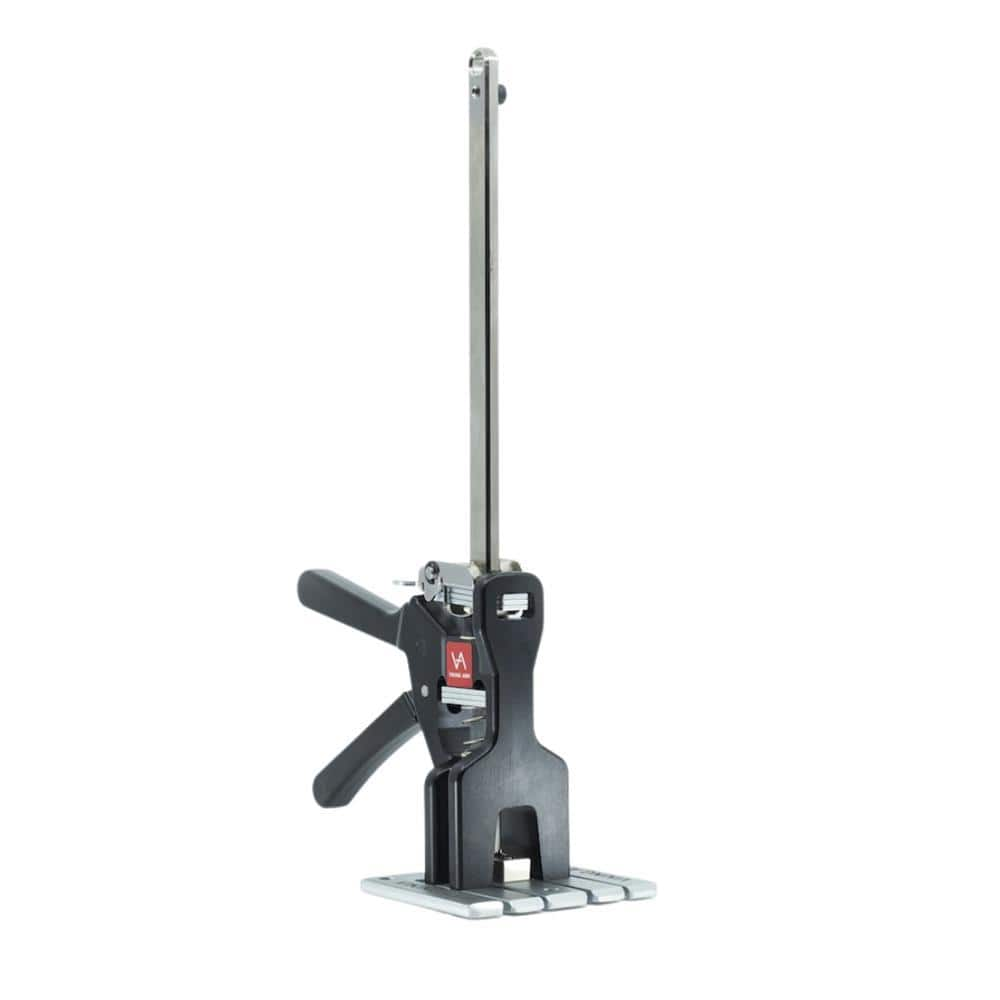
The Ultimate Guide to Handing Lifting Tool Jacks
The Ultimate Guide to Hand Lifting Tool Jacks
Hand jacks are essential equipment for mechanics, DIY enthusiasts and professionals. These versatile tools make lifting objects easier and safer. This guide explores the world of hand jacks, their types, uses and best practices for 2024.
Translation results
Translation result
What Is a Hand Lifting Tool Jack?
A hand lifting tool jack is a portable device that lifts heavy loads. It uses mechanical advantage to multiply human force. These jacks come in various sizes and capacities. They’re commonly used in automotive repair, construction, and industrial settings.
Types of Hand Lifting Tool Jacks
Hydraulic Bottle Jack
Hydraulic bottle jacks are compact and powerful. They use hydraulic fluid to generate lifting force. These jacks have a vertical design resembling a bottle. They’re ideal for lifting vehicles and heavy machinery.
Scissor Jack
Scissor jacks use a screw mechanism to extend or retract. Their design resembles a pair of scissors. They’re often included as standard equipment in cars. Scissor jacks are lightweight and easy to store.
Floor Jack
Floor jacks are low-profile jacks on wheels. They use hydraulic power for Hand Grabber Tool. These jacks are popular in automotive shops. They allow for easy positioning under vehicles.
Hi-Lift Jack
Hi-lift jacks are versatile tools with a long, vertical design. They can lift, winch, clamp, and spread. These jacks are popular among off-road enthusiasts. They’re useful for vehicle recovery in challenging terrains.
How Hand Lifting Tool Jacks Work
Hand lifting tool jacks operate on simple mechanical principles. They convert a small input force into a large output force. This conversion happens through various mechanisms:
Hydraulic jacks use Pascal’s principle. They transfer force through an incompressible fluid. A small piston creates high pressure in the fluid. This pressure acts on a larger piston, generating significant lifting force.Screw jacks use the mechanical advantage of screws. Turning the screw creates vertical movement. This design is simple and reliable. It’s commonly found in scissor jacks.
Some jacks, like hi-lift jacks, use levers. The long handle acts as a lever. It multiplies the user’s input force. This design allows for hand jack lift tool capacity with manual effort.
Choosing the Right Hand Lifting Tool Jack
Consider the maximum weight the jack needs to lift. Always choose a jack rated higher than your heaviest load. This ensures safety and prevents overloading.Different jacks offer varying lift heights. Consider the maximum height needed for your tasks. Floor jacks typically have lower lift heights than bottle jacks.
If you need to move the jack frequently, consider its weight and size. Scissor jacks are highly portable. Hydraulic floor jacks are heavier but offer more stability.Look for jacks made from high-quality materials. Steel construction offers durability. Check for rust-resistant finishes for longevity.
Prioritize jacks with built-in safety mechanisms. Overload protection and safety valves prevent accidents. Some jacks feature locking mechanisms for added security.
Using Hand Lifting Tool Jacks Safely
Always use jacks on a flat, stable surface. Uneven ground can cause the jack to tip or slip. This can lead to serious accidents.Position the jack at the correct lifting points. Refer to your vehicle’s manual for specific locations. Improper placement can damage the vehicle or cause instability.
Never rely solely on a jack to support a hand weeding tool. Always use jack stands for additional support. This prevents accidents if the jack fails.Inspect your jack regularly for wear and damage. Check for fluid leaks in hydraulic jacks. Keep moving parts lubricated for smooth operation.
Never exceed the jack’s rated capacity. Overloading can cause catastrophic failure. It puts both the equipment and user at risk.Operate the jack slowly and smoothly. Avoid jerky movements. This ensures better control and reduces the risk of accidents.
Maintenance Tips for Hand Lifting Tool Jacks
Clean your jack after each use. Remove dirt, grease, and debris. This prevents contamination of moving parts.Apply lubricant to moving parts regularly. This reduces friction and wear. Use manufacturer-recommended lubricants for best results.
For hydraulic jacks, check the fluid level periodically. Top up if necessary. Use the correct type of hydraulic fluid.Store your jack in a dry, clean area. Protect it from extreme temperatures and moisture. This prevents rust and deterioration.
Regularly inspect your jack for signs of wear or damage. Check for cracks, bends, or loose components. Address any issues promptly.
Common Uses of Hand Lifting Tool Jacks
Jacks are essential for vehicle maintenance. They allow access to undercarriage components. Mechanics use them for tire changes, brake repairs, and oil changes.Construction workers use jacks for lifting and positioning heavy materials. They’re useful for aligning beams and adjusting structures.
Factories use jacks for machinery maintenance. They help in hand tool sets and positioning heavy equipment. Jacks facilitate repairs and replacements in tight spaces.Homeowners use jacks for various tasks. They’re helpful in furniture moving, appliance installation, and home repairs.
Farmers use jacks to maintain and repair heavy machinery. They’re crucial for tasks like changing tractor tires.Hi-lift jacks are popular among off-road enthusiasts. They help in vehicle recovery in challenging terrains. These jacks can lift vehicles out of mud or sand.
Innovations in Hand Lifting Tool Jack Technology
Manufacturers are exploring lightweight, high-strength materials. These make jacks more portable without sacrificing strength.Some modern jacks incorporate sensors and digital displays. They provide real-time information on weight and lift height. This enhances safety and precision.
Versatile jacks that serve multiple purposes are gaining popularity. They combine lifting, spreading, and winching capabilities in one tool.Manufacturers focus on ergonomic designs. They aim to reduce user fatigue and improve comfort during operation.
Some jacks now feature electric motors. These assist in lifting heavy loads with minimal manual effort. They’re especially useful in industrial settings.
Comparing Hand Lifting Tool Jacks to Alternatives
While hand lifting tool jacks are versatile, other lifting methods exist:
Hoists
Hoists use chains or cables for lifting. They’re suitable for hand grinder tool. Hoists are common in warehouses and construction sites.
Cranes
Cranes offer high lifting capacity and reach. They’re used for heavy loads and high lifts. Cranes are essential in large construction projects.
Forklifts
Forklifts combine lifting and transportation. They’re efficient for moving palletized loads. Forklifts are common in warehouses and shipping yards.
Pneumatic Lifts
These use compressed air for lifting. They’re popular in automotive shops. Pneumatic lifts offer stable, hands-free operation.
Environmental Considerations
Manual jacks require no electricity. This makes them energy-efficient compared to powered alternatives.Well-maintained jacks can last for decades. This reduces waste and the need for frequent replacements.Many jacks are made from recyclable materials like steel. At the end of their life, they can be recycled to reduce environmental impact.Hydraulic jacks require proper disposal of used fluid. Follow local regulations for environmentally safe disposal.
Precautions for using hand lifting tool jack
Choose the Right Jack:
Before using a hand lifting tool, it is essential to select the right type of jack for the specific task at hand. There are various types of jacks available, including floor jacks, bottle jacks, scissor jacks, and hydraulic jacks. Each type has its own weight capacity and purposes. Choose a jack that matches the weight and size requirements of the object or vehicle you intend to rust off tools.
Safety and Stability:
When using a hand lifting tool, safety and stability are paramount. Follow these guidelines to ensure safe operation:
- Find a stable and level surface to place the jack to minimize the risk of tipping or instability during lifting.
- Position the jack on a hard surface, avoiding loose or slippery ground.
- Do not place any body parts beneath the lifted object or vehicle to prevent serious injuries in the event of a collapse or slip.
Weight Capacity:
Before lifting an object with a jack, review the weight capacity indicated by the manufacturer. Exceeding the weight limit can potentially damage the lifting tool, causing it to fail and posing a risk of injury. Always ensure that the weight of the load or vehicle being lifted does not exceed the specified capacity of the jack.
Proper Setup and Positioning
Correct setup and positioning of the jack are essential for safe and effective lifting. Follow these steps:
- Place the jack on a designated jack point specified in the vehicle’s manual or instructions.
- Ensure that the lifting area is clear of any obstacles or loose objects that could interfere with the jack’s functionality or cause instability.
- Position the jack’s lifting arm or platform directly beneath the designated lifting point, providing equal support on both sides.
Conclusion
Hand lifting tool jacks are indispensable in many industries and personal applications. They offer a simple yet effective solution for hand tools heavy loads. Understanding their types, uses, and safety measures is crucial for anyone working with these tools.
As technology advances, hand lifting tool jacks continue to evolve. They become safer, more efficient, and more versatile. However, the basic principles remain the same. These tools exemplify the power of simple mechanics in solving complex lifting challenges.
Whether you’re a professional mechanic, a DIY enthusiast, or someone who occasionally needs to lift heavy objects, hand lifting tool jacks are invaluable. They empower users to tackle tasks that would otherwise be impossible or dangerous. With proper use and maintenance, these tools will continue to be reliable lifting solutions for years to come.
Remember, safety always comes first when using hand lifting tool jacks. Proper training, regular maintenance, and adherence to safety guidelines are essential. These practices ensure that these powerful tools remain assets rather than liabilities in any workplace or personal project.